
Â
Radial needle roller and cage assemblies:
- are suitable for applications with a very small radial design envelope, where the raceways on the shaft and in the housing are designed as rolling bearing raceways (direct bearing arrangement)
- can support high radial loads
- allow high speeds
- combine the load carrying capacity advantages of full complement needle roller bearing arrangements with the speed advantages of a cage bearing
- have a high running accuracy
- result in rigid bearing arrangements
- are easy to mount
- permit technically straightforward, economical and cost-effective designs
Radial needle roller and cage assembly – comparison of radial design envelope with drawn cup needle roller bearing with open ends and machined needle roller bearing
 Radial needle roller and cage assembly
 Drawn cup needle roller bearing with open ends
 Machined needle roller bearing
|
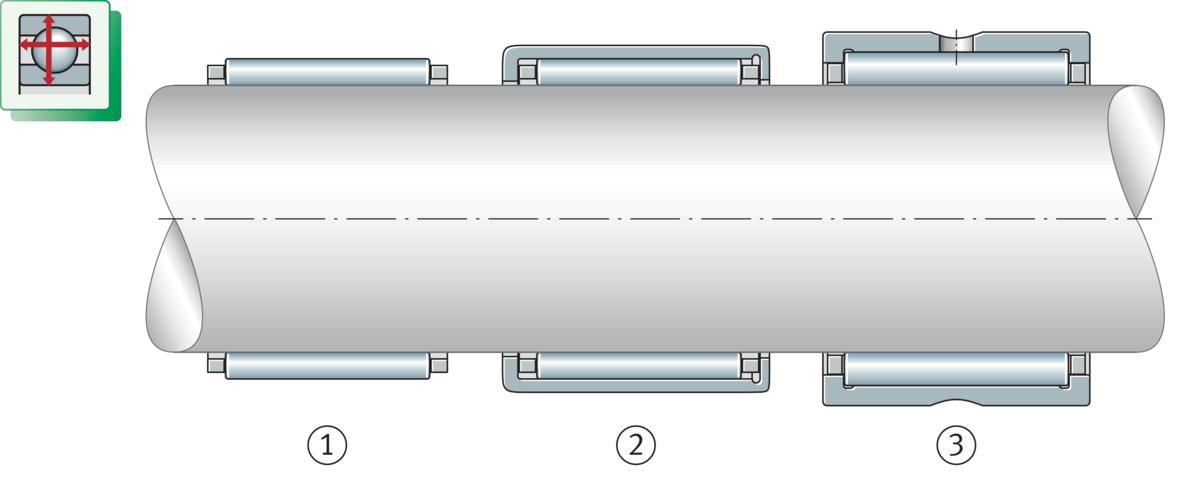 |
Design variants
Radial needle roller and cage assemblies:
Needle roller and cage assemblies of basic design
Bearings with a very small radial section height
Needle roller and cage assemblies are part of the group of radial needle roller bearings. These ready-to-fit bearing arrangement elements comprise needle cages, which are fitted with needle rollers ➤ Figure and ➤ Table. They are rolling bearings with a very small radial section height and, apart from full complement needle roller bearing arrangements, are the simplest design of radial needle roller bearing. However, while the design envelope is completely filled with loose needle rollers in full complement needle roller bearing arrangements and, depending on the position, the rolling elements are therefore in contact with each other, these are guided in the cage pockets in needle roller and cage assemblies. The pockets, which are separated from each other by bars and are uniformly distributed around the circumference of the cage, maintain the spacing of the rolling elements relative to each other. The cage and rolling elements thus create a ready-to-fit unit.
The needle rollers are guided parallel to the axis
In addition, the bars prevent sliding friction between adjacent rolling elements and guide the rolling elements parallel to the bearing axis in the load-free zone. Guidance parallel to the axis prevents skewing of the needle rollers in the load-free zone. Compared with full complement needle roller bearing arrangements, needle roller and cage assemblies are suitable for higher speeds. As a result, the cage compensates for the disadvantages of a full complement needle roller bearing arrangement.
For bearing arrangements with a particularly small radial design envelope
Standard needle roller sorts are used as needle rollers ➤ Table. Due to the absence of an inner and outer ring, the radial section height of the bearings is only equivalent to the diameter of the needle rollers. As a result, needle roller and cage assemblies are particularly suitable for applications requiring only a very small radial design envelope. The majority of the bearings are of a single row design ➤ Figure. This variant has the prefix K.
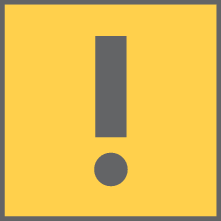
Needle roller and cage assemblies are only functional once they have been fitted between the housing and shaft. In this case, the raceways must be designed as rolling bearing raceways ➤ section.
Single row needle roller and cage assembly
Fr = radial load
|
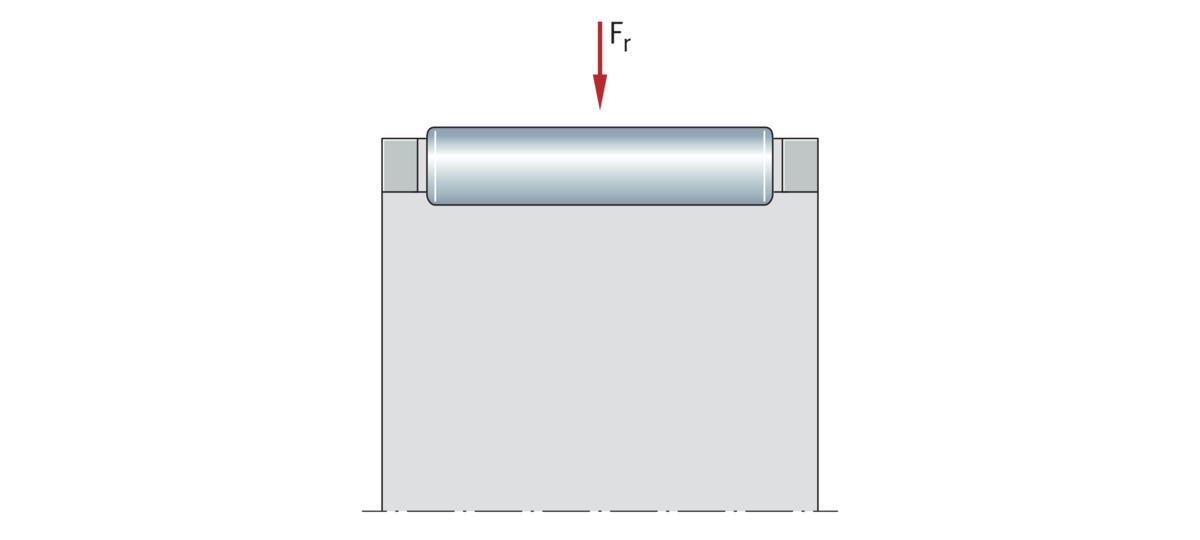 |
Double row needle roller and cage assemblies
Particularly high radial load carrying capacity
Double row needle roller and cage assemblies have a higher load carrying capacity than single row designs, but are correspondingly wider ➤ Figure. These bearings have the prefix Kand the suffix ZW and are only available in particular enveloping circle diameters Fw ➤ section and ➤ link.
Double row needle roller and cage assembly
Fr = radial load
|
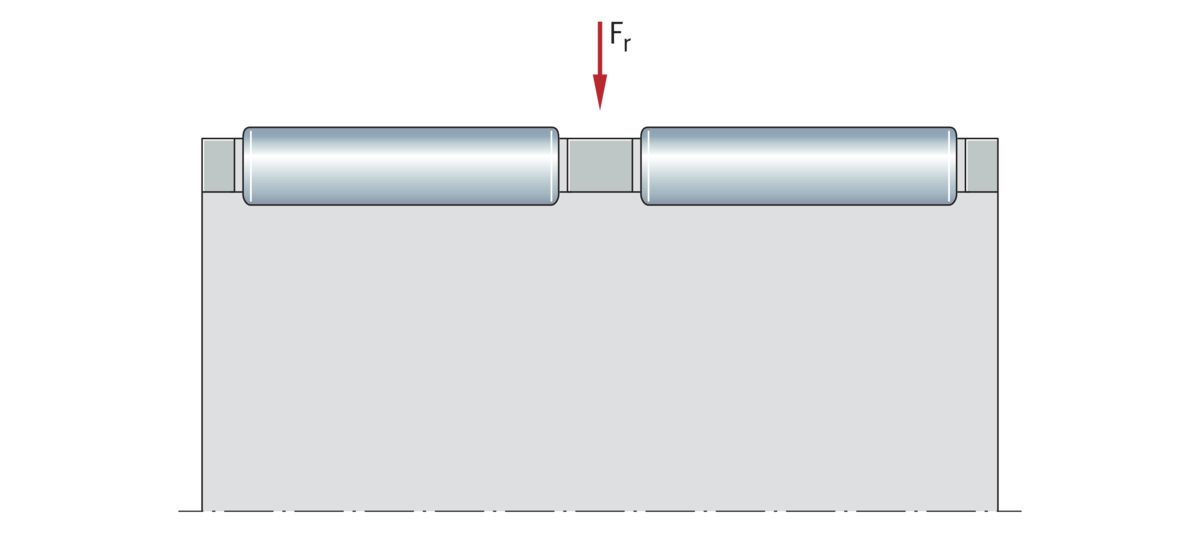 |
Needle rollers
Standard needle roller sorts are used as needle rollers
Needle roller and cage assemblies are supplied with standard needle roller sorts of grade G2 in accordance with the table ➤ Table. In all cases, needle rollers of only one sort are used in any one needle roller and cage assembly. The sort is printed on the packaging and colour coded ➤ Table. The sorts are designated by the upper and lower deviations (in μm), the diameter tolerance is a maximum of 2 μm. In each case, two neighbouring needle roller sorts are matched as sort pairs.
Dimensional and geometrical accuracy of needle rollers of grade G2
Grade
|
Deviations and tolerances for diameter Dw1)
|
Length tolerance
|
Deviation
|
Variation of needle roller diameter within a single sort
|
Sort pair colour code
|
Sorts
|
Roundness
|
Roughness
|
VDwL
|
|
|
tDw
|
Ra
|
|
μm
|
μm
|
|
μm
|
μm
|
μm
|
|
max.
|
|
|
max.
|
max.
|
|
G2
|
0 – 7
|
2
|
red
|
0
|
-2
|
-1
|
-3
|
1
|
0,1
|
h13
|
G2 |
0 – 7 |
2 |
blue
|
-2
|
-4
|
-3
|
-5
|
1 |
0,1 |
h13 |
G2 |
0 – 7 |
2 |
white (grey)
|
-4
|
-6
|
-5
|
-7
|
1 |
0,1 |
h13 |
- The tolerance values apply to the centre point of the needle roller.
Needle roller and cage assemblies for centrifugal forces and high acceleration forces (KZK, KBK)
Needle roller and cage assemblies for connecting rod bearing arrangements
Designed for piston pin and crank pin bearing arrangements
Needle roller and cage assemblies for connecting rod bearing arrangements are used in the crank mechanisms of 2 and 4 stroke combustion engines as well as in compressors, for supporting crank pins and piston pins ➤ Figure. These cages support high centrifugal and acceleration forces and are suitable for high speeds.
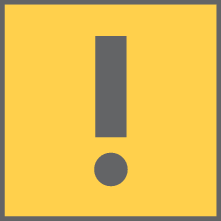
For piston pin bearing arrangements, only needle roller and cage assemblies with the designation KZK and KBK may be used TPI 94. As catalogue needle roller and cage assemblies of type K are not designed to accommodate loads generated by centrifugal forces and high acceleration forces, non-compliance may result in failures.
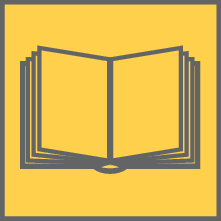
The needle roller and cage assemblies for piston pin and crank pin bearing arrangements are described in detail in Technical Product Information TPI 94. This publication can be requested from Schaeffler.
Crank pin and piston pin bearing arrangement
 Needle roller and cage assembly for crank pins, externally guided
 Needle roller and cage assembly for piston pins, internally guided
|
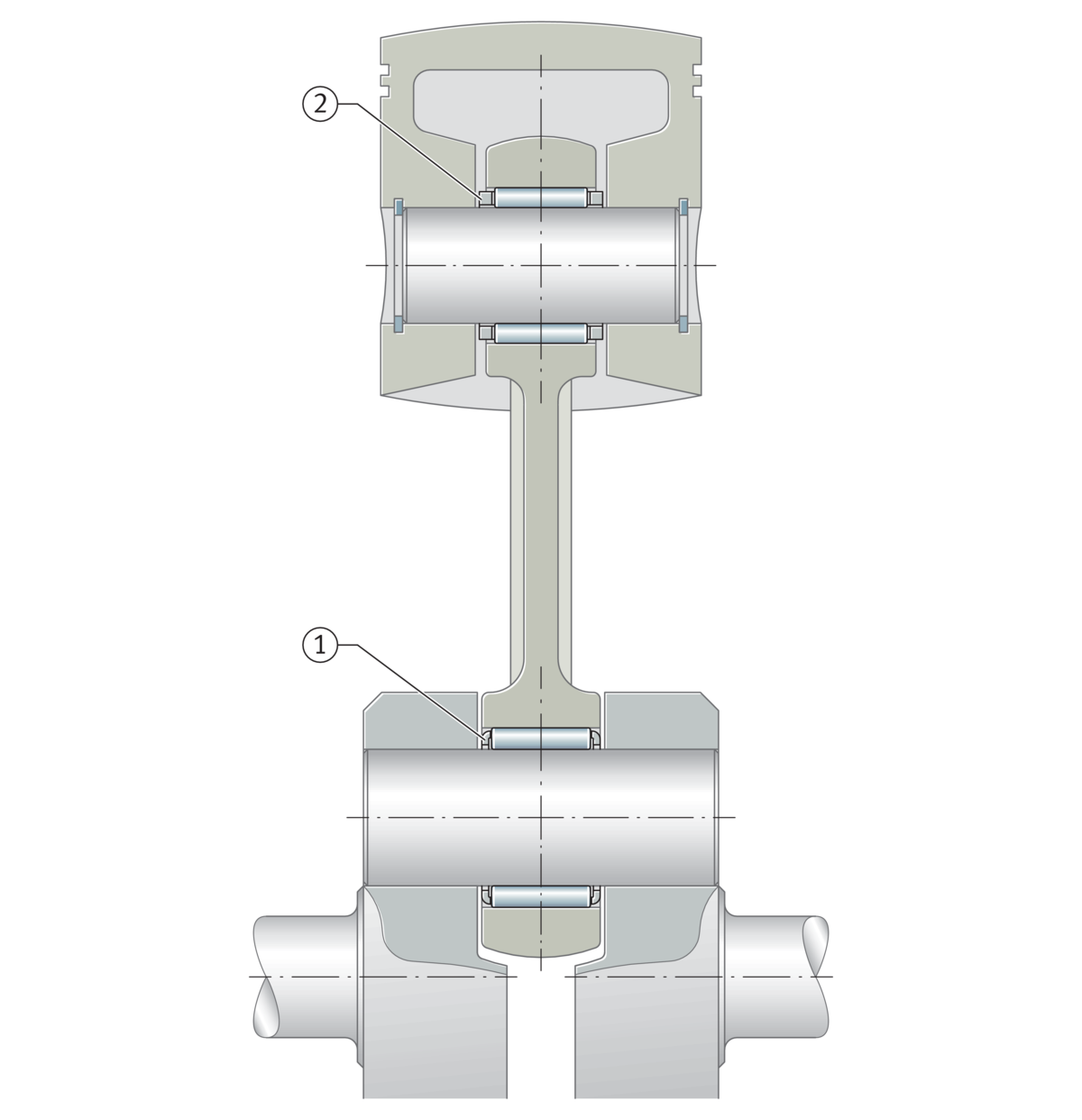 |
Needle roller and cage assemblies for crank pins (KZK)
Needle roller and cage assemblies for crank pins (series KZK) are externally guided, which means that the connecting rod bore guides the cage radially with little clearance ➤ Figure. The radial movement of the cage in relation to the connecting rod bore and the rolling elements is as small as possible. The cages are made from quenched and tempered steel, have good wear resistance, high strength and large guidance surfaces which are designed for optimum lubrication.
Needle roller and cage assemblies for piston pins (KBK)
The needle roller and cage assemblies for piston pins (series KBK) are internally guided, which means that the piston pin guides the cage radially with little clearance ➤ Figure. Due to the small radial internal clearance, tilting of the connecting rod is reduced to a minimum. The bearings support high-frequency oscillating loads and are available for the majority of piston pin diameters in various widths, in accordance with the piston pin abutment distance. The low-wear steel cages are case hardened or quenched and tempered and have high strength.
Needle roller and cage assemblies for planetary gear bearing arrangements (KZK)
Needle roller and cage assemblies for planetary gear bearing arrangements
Needle roller and cage assemblies are also used for applications in planetary gearing arrangements, such as automatic gearboxes ➤ Figure. As very high speeds, as well as centrifugal and acceleration forces, can occur in planetary gear bearing arrangements and the cage is therefore subject to high demands, the responsible Application Engineering and Design functions should select or design a suitable needle roller and cage assembly. In such cases, please consult Schaeffler.
Planetary gear bearing arrangement
|
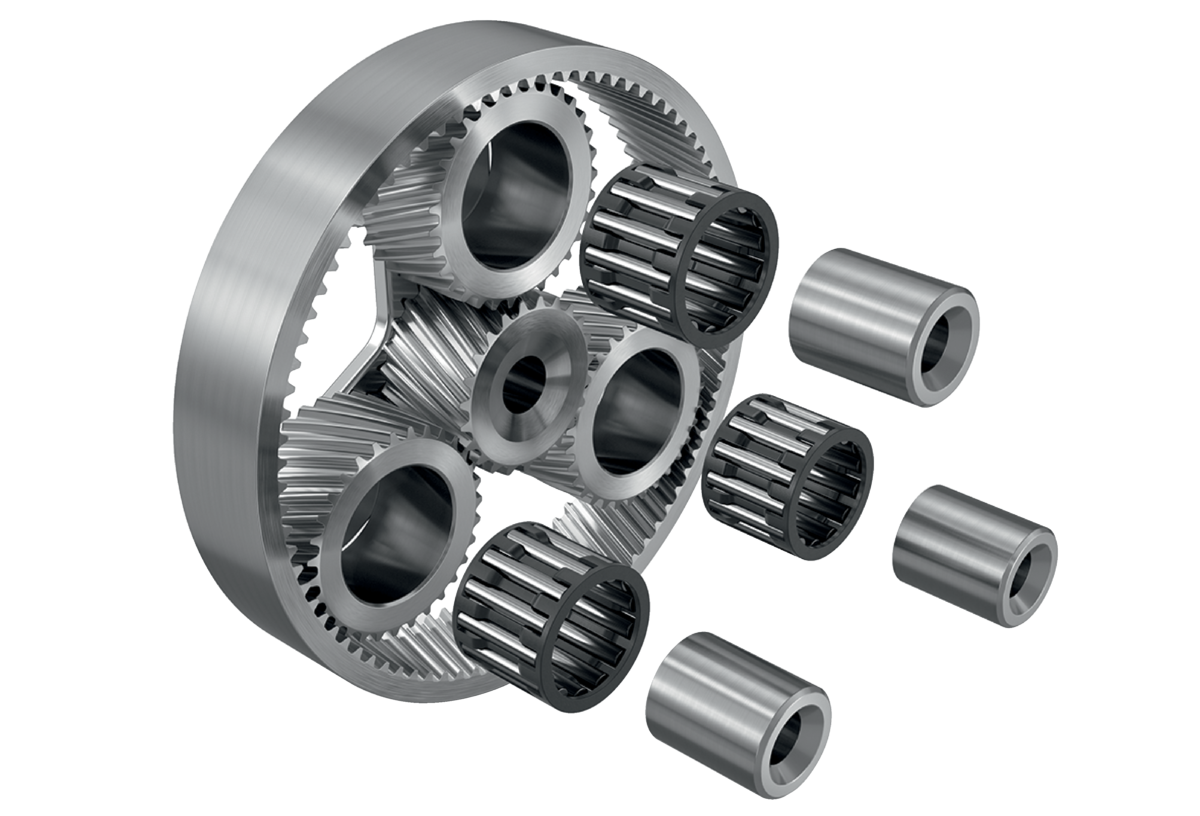 |
Needle roller and cage assemblies customised from profiled strip (K)
Customised radial needle roller and cage assemblies for specific requirements
These radial needle roller and cage assemblies are produced by bending flat cages BF and fitted with needle rollers after forming ➤ Figure. As a result, it is possible to achieve simple designs of clearance-free bearing arrangements with high running accuracy, load carrying capacity and speed suitability, in combination with very small radial and axial section height. Due to their high radial runout accuracy, the bearings are also suitable for precision applications. Since the needle roller and cage assemblies are not tied to defined dimension series but can be precisely produced to a wide range of diameter values in accordance with the specific application (shaft diameter of 105 mm to 1 000 mm), they are an economical alternative to catalogue standard bearings. They are normally supplied bent into their final shape but can also be formed by the customer from BF flat cages. After forming, there is an open joint ➤ Figure. As a result, radial needle roller and cage assemblies can be easily mounted in recessed raceways. The function of the cages is not impaired by the opening.
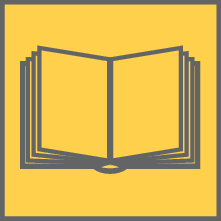
BF flat cages and radial needle roller and cage assemblies produced from BF flat cages are described in detail in Technical Product Information TPI 203. This publication can be requested from Schaeffler.
Radial needle roller and cage assembly produced by bending from a flat cage BF
 Open joint
|
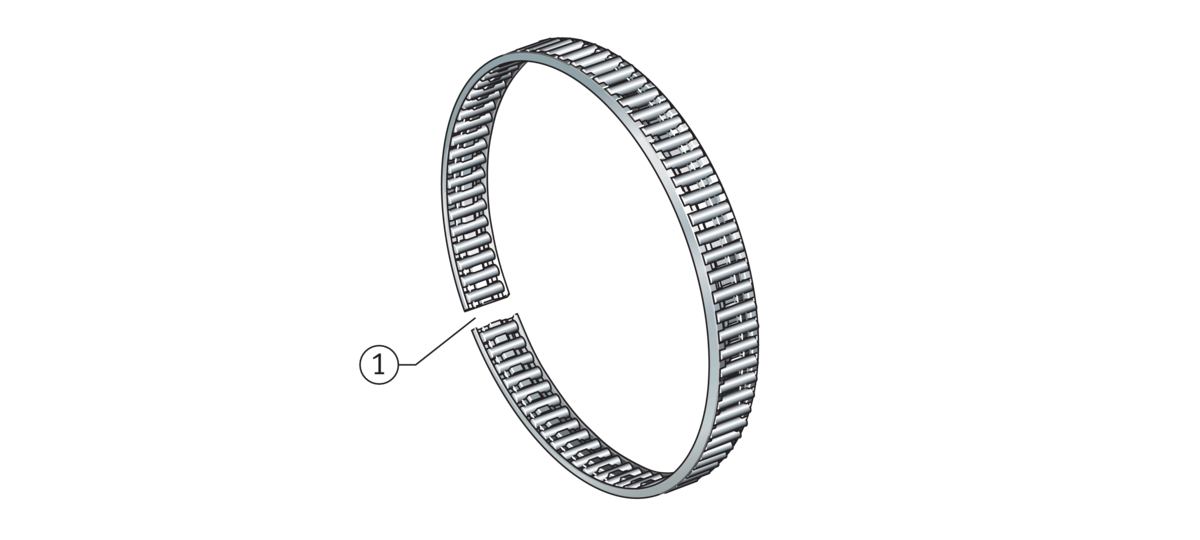 |
Capable of supporting high radial loads, but not axial loads
Due to the line contact of the needle rollers, needle roller and cage assemblies are suitable for supporting high radial loads. In contrast to the ball, the needle has a larger contact area perpendicular to its axis. As a result, it can transmit higher forces, has greater rigidity and can support the same loads with smaller rolling element diameters. Due to the needle roller set, double row bearings have a particularly high radial load carrying capacity. They are used when the load carrying capacity of single row bearings is no longer sufficient.
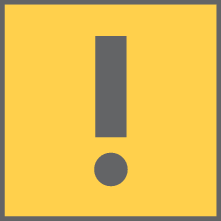
Needle roller and cage assemblies cannot support axial forces ➤ section. For axial loads, they can be combined with a bearing which is capable of supporting axial load, such as a deep groove ball bearing or a cylindrical roller bearing with axial load carrying capacity. In such cases, the axial bearing is arranged adjacent to the needle roller and cage assembly ➤ Figure.
Passenger car gearbox: bearing arrangement of main shaft
A – E = bearing positions
 Cylindrical roller bearing and cage assembly as pilot bearing (non-locating bearing)
 Deep groove ball bearing (locating bearing, capable of supporting axial loads)
 Needle roller and cage assembly (non-locating bearing, capable of supporting radial loads only)
|
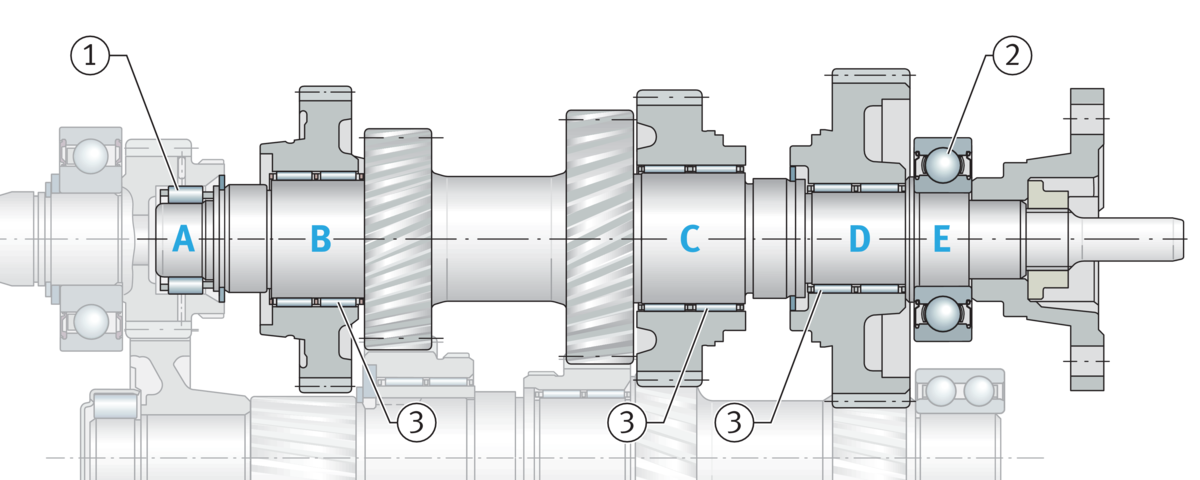 |
The bearings are not suitable for the compensation of shaft misalignments relative to the housing bore
Needle roller and cage assemblies are not suitable for the compensation of angular misalignments. The extent to which a misalignment of the shaft can be tolerated relative to the housing bore is dependent on factors such as the design of the bearing arrangement, the size of the bearing, the operating clearance and the load. As a result, no guide value can be specified here for a possible misalignment.
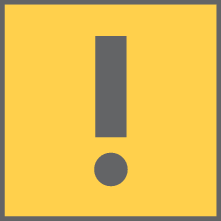
In all cases, misalignments cause increased running noise, place increased strain on the cages and have a harmful influence on the operating life of the bearings.
Oil or grease lubrication is possible
Needle roller and cage assemblies are not greased. In order to prevent direct metallic contact between rolling elements, raceways and cages, they must be lubricated. Oil or grease lubrication is suitable. The lubricant reduces the wear and also protects the surfaces against corrosion. The choice of lubricant is essentially dependent on the operating temperatures and speeds, but is also influenced by other factors.
The use of oil lubrication is preferred
For most applications involving needle roller and cage assemblies, oil should be used in preference as the lubricant.
Compatibility with plastic cages
When using bearings with plastic cages, compatibility between the lubricant and the cage material must be ensured if synthetic oils, lubricating greases with a synthetic oil base or lubricants containing a high proportion of EPÂ additives are used.
Observe oil change intervals
Aged oil and additives in the oil can impair the operating life of plastics at high temperatures. As a result, stipulated oil change intervals must be strictly observed.
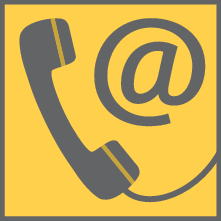
If there is any uncertainty regarding the suitability of the selected lubricant for the application, please consult Schaeffler or the lubricant manufacturer.
The bearings are of an open design
Needle roller and cage assemblies are supplied without seals. As a result, sealing of the bearing position must be carried out in the adjacent construction. This must reliably prevent:
- moisture and contaminants from entering the bearing
- the egress of lubricant from the bearing position
Limiting speeds and reference speeds in the product tables
The product tables give two speeds for the bearings:
- the kinematic limiting speed nG
- the thermal speed rating nϑr
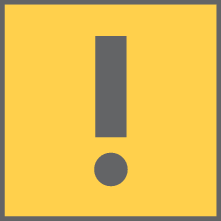
The limiting speed nG is the kinematically permissible speed of a bearing. Even under favourable mounting and operating conditions, this value should not be exceeded without prior consultation with Schaeffler ➤ link. The values in the product tables are valid for oil lubrication.
Values for grease lubrication
For grease lubrication, 60% of the value stated in the product tables is permissible in each case.
Reference speeds
nϑr is used to calculate nϑ
The thermal speed rating nϑr is not an application-oriented speed limit, but is a calculated ancillary value for determining the thermally safe operating speed nϑ ➤ link.
Schaeffler Noise Index
The Schaeffler Noise Index (SGI) is not yet available for this bearing type ➤ link. The data for these bearing series will be introduced and updated in stages.
Limiting values
The operating temperature of the bearings is limited by:
- the dimensional stability of the rolling elements
- the cage
- the lubricant
Possible operating temperatures of needle roller and cage assemblies ➤ Table.
Permissible temperature ranges
Operating temperature
|
Needle roller and cage assemblies
|
with plastic cage
|
with sheet steel cage and with cages made from copper-zinc alloy
|
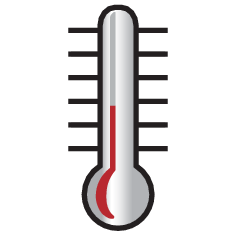
|
–20 °C to +120 °C
|
–30 °C to +140 °C
|
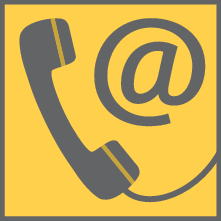
In the event of anticipated temperatures which lie outside the stated values, please contact Schaeffler.
The standard cages are made from sheet steel
The standard cages are made from sheet steel and, with an enveloping circle diameter Fw ≧ 195 mm, from a copper-zinc alloy. Bearings with a plastic cage are only available in particular sizes and have the suffix TV ➤ Table and ➤ link. Other cages are available by agreement. With such cages, however, suitability for high speeds and temperatures as well as the basic load ratings may differ from the values for the bearings with standard cages.
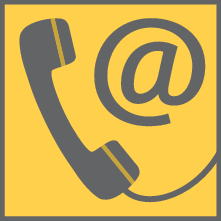
For high continuous temperatures and applications with difficult operating conditions, bearings with sheet steel cages should be used. If there is any uncertainty regarding cage suitability, please consult Schaeffler.
Radial internal clearance
Influencing factors on the radial internal clearance
The radial internal clearance can be influenced by the needle roller sort as well as by the shaft and housing tolerances. When standard needle roller sorts are used, a radial internal clearance of C2 to CN is achieved (radial internal clearance for needle and cylindrical roller bearings to DIN 620-4), if the shaft and housing tolerances are observed ➤ Table and normal operating conditions are present. If the actual dimensions have a plus tolerance, a radial internal clearance of 0 can be achieved.
Checking the enveloping circle diameter
Fw can only be checked in a mounted condition
The inner and outer enveloping circle diameters Ew and Fw cannot be measured in an unmounted condition. As a result, the function of the bearings is checked using plug gauges and locating rings in accordance with the methods indicated in DIN 620-1/ISO 1132-2. In order to carry out the check, the needle roller and cage assemblies are placed in a locating ring, which corresponds to the specific nominal dimension Ew of the needle roller and cage assembly. The function of the needle roller and cage assembly is ensured if the plug gauge, which corresponds to the nominal dimension Fw, can be inserted and rotated without jamming.
Dimension standards
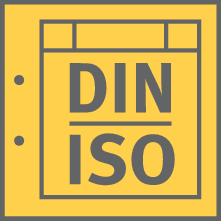
The main dimensions of single row needler roller and cage assemblies correspond to DIN 5405-1:2016 and ISO 3030:2011, where standardised.
Tolerances
Needle rollers
The needle rollers correspond to DIN 5402-3:2012 and ISO 3096:1996. The diameters of all needle rollers in a needle roller and cage assembly lie within the tolerance of 2 μm ➤ Table.
Width Bc
The deviations for cage width Bc are as follows for all needle roller and cage assemblies: Bc –0,2/–0,8 ➤ link.
For a description of the suffixes used in this chapter ➤ Table and medias interchange http://www.schaeffler.de/std/1B69.
Suffixes and corresponding descriptions
Suffix
|
Description of suffix
|
TV
|
Cage made from glass fibre reinforced polyamide PA66
|
Standard
|
ZW
|
Double row design (only available in certain enveloping circle diameters)
|
Standard |
The designation of bearings follows a set model. Examples ➤ Figure and ➤ Figure. The composition of designations is subject to DIN 623-1 ➤ Figure.
Single row needle roller and cage assembly: designation structure
|
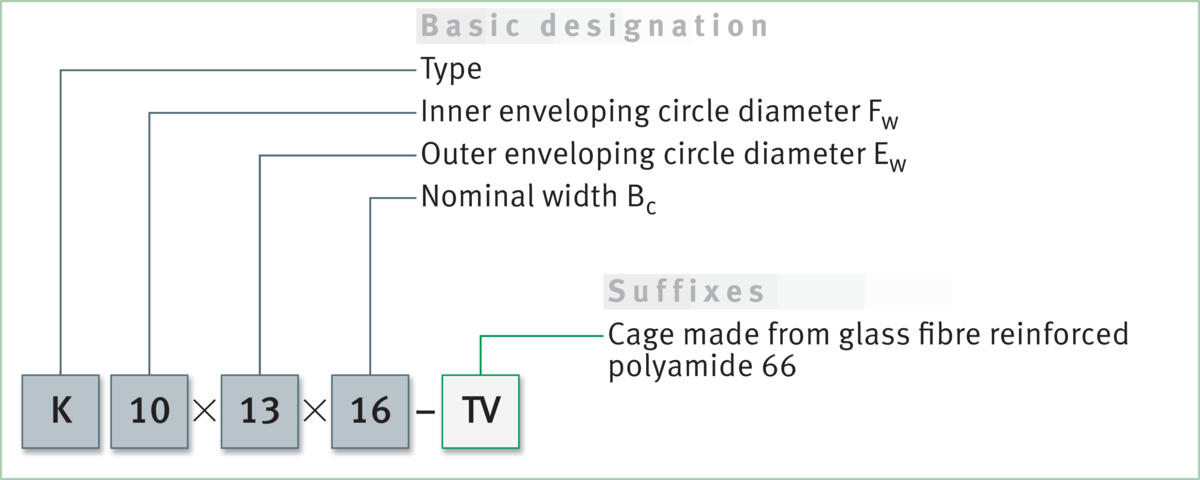 |
Double row needle roller and cage assembly: designation structure
|
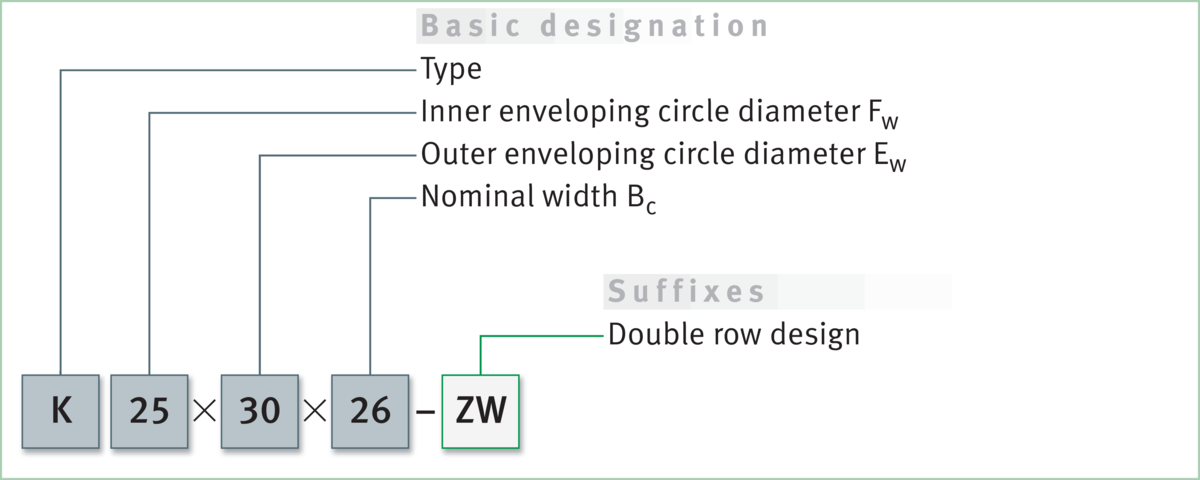 |
Equivalent dynamic bearing load
P = Fr under purely radial load of constant magnitude and direction
The basic rating life equation L = (Cr/P)p used in the dimensioning of bearings under dynamic load assumes a load of constant magnitude and direction. In radial bearings, this is a purely radial load Fr. If this condition is met, the bearing load Fr is used in the rating life equation for P (P = Fr).
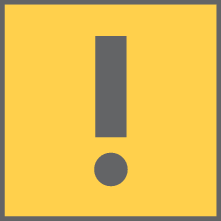
Needle roller and cage assemblies can only support radial loads. Thus, for these bearings ➤ Equation.
Equivalent dynamic load
Legend
P |
N |
Equivalent dynamic bearing load
|
Fr |
N |
Radial load
|
Equivalent static bearing load
For needle roller and cage assemblies subjected to static load ➤ Equation.
Equivalent static load
Legend
P0 |
N |
Equivalent static bearing load
|
F0r |
N |
Largest radial load present (maximum load)
|
Static load safety factor
S0Â =Â C0/P0
In addition to the basic rating life L (L10h), it is also always necessary to check the static load safety factor S0 ➤ Equation.
Static load safety factor
Legend
S0 |
- |
Static load safety factor
|
C0 |
N |
Basic static load rating
|
P0 |
N |
Equivalent static bearing load
|
In order to prevent damage due to slippage, a minimum radial load of P > C0r/60 is required
In order that no slippage occurs between the contact partners, the needle roller and cage assemblies must be constantly subjected to a sufficiently high load. Based on experience, a minimum radial load of the order of P > C0r/60 is thus necessary. In most cases, however, the radial load is already higher than the requisite minimum load due to the weight of the supported parts and the external forces.
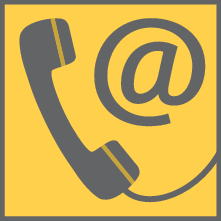
If the minimum radial load is lower than indicated above, please consult Schaeffler.
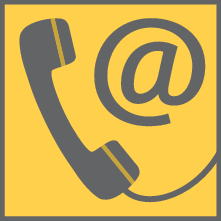
The shaft and housing design and the lateral restriction (axial location) of the bearing position is crucial to the correct function of needle roller and cage assemblies ➤ Table, ➤ Figure and ➤ Figure.
Raceways for bearings without inner and/or outer ring (direct bearing arrangement)
Produce the raceway as a rolling bearing raceway
If the needle roller and cage assemblies run directly on the shaft and/or in the housing bore (so-called direct bearing arrangement), then the raceway for the rolling elements on the shaft and in the housing must be produced as a rolling bearing raceway (hardened and ground). Design of raceways ➤ Table. The surface hardness of the raceways must be 670 HV to 840 HV, the hardening depth CHD or SHD must be sufficiently large. The values in the table refer to commonly encountered application examples. If the shaft cannot be produced as a raceway, the needle roller and cage assemblies can be combined with Schaeffler bearing rings. However, the section height of the bearings will then be increased by the thickness of the rings.
Tolerance classes and surface design of raceways for needle roller and cage assemblies (direct bearing arrangement)
Shaft diameter
|
Bore tolerance1)
|
Shaft tolerance1)
|
Design of raceway
|
Recommended mean roughness value
|
Roundness tolerance
|
Parallelism tolerance
|
Nominal dimension
|
Operating clearance
|
Ramax (Rzmax)
|
mm
|
over
|
incl.
|
small
|
normal
|
large
|
μm
|
max.
|
max.
|
‒
|
80 |
G6 |
j5 |
h5 |
g6 |
0,2Â (1) |
IT3 |
IT3 |
- |
80 |
H6 |
h5 |
g5 |
f6 |
0,2 (1) |
80 |
120 |
G6 |
h5 |
g5 |
f6 |
0,3 (1,6) |
120 |
- |
G6 |
h5 |
g5 |
f6 |
0,4 (2,5) |
120 |
- |
H6 |
- |
f5 |
e6 |
0,4 (2,5) |
- The envelope requirement â’º applies.
Raceway width for direct bearing arrangement and axial running surfaces
Mounting dimensions for needle roller and cage assemblies and surface quality of the running surfaces
The raceway width must be at least equal to the nominal width Bc (Bc is produced with a (–) tolerance); values for Bc ➤ link and ➤ Figure. The spacing between the axial running surfaces of the cage must be sufficiently large. The spacing dimension for running surfaces is given as Bc H12 Ⓔ, in order to avoid jamming of the needle roller and cage assemblies (H12 in accordance with ISO 286-2). The lateral running surfaces for the needle roller and cage assemblies must be designed as precision machined (Ramax 2 recommended) and wear-resistant ➤ Figure. Interruptions in the running surfaces should be avoided.
Example
For a design envelope of Bc = 10 mm, a needle roller and cage assembly with the nominal width Bc = 10 mm is suitable, as the maximum cage width is 9,8 (0/–0,6) mm.
Raceway width and axial running surfaces for needle roller and cage assemblies
Bc H12 = nominal width
Bc –0,2/–0,8 = cage width
Ramax = maximum roughness of running surfaces
 Location by means of shaft shoulder, axial washer and snap ring
 Axial washer
 Snap ring
|
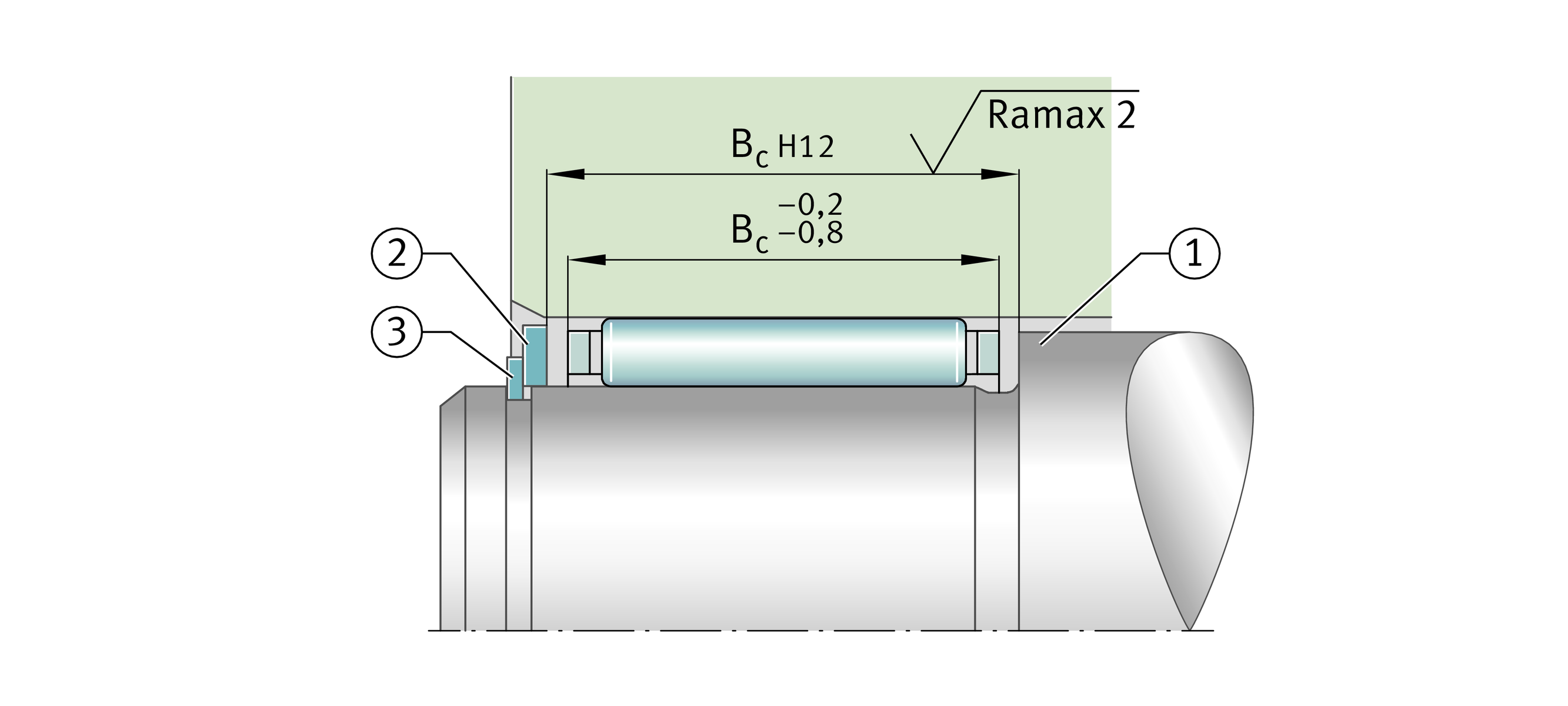 |
Axial guidance and location of needle roller and cage assemblies
Guidance can be provided by the shaft or on the housing
Needle roller and cage assemblies must be axially guided and located. Guidance can be provided by the shaft or on the housing ➤ Figure and ➤ Figure. Snap rings or an appropriately designed adjacent construction are suitable for this purpose. If location is by means of snap rings or retaining rings, a washer must be arranged in front of the rings➤ Figure. The overlap between the ring and washer must be sufficiently large.
Axial location by means of housing parts (lateral guidance on housing)
|
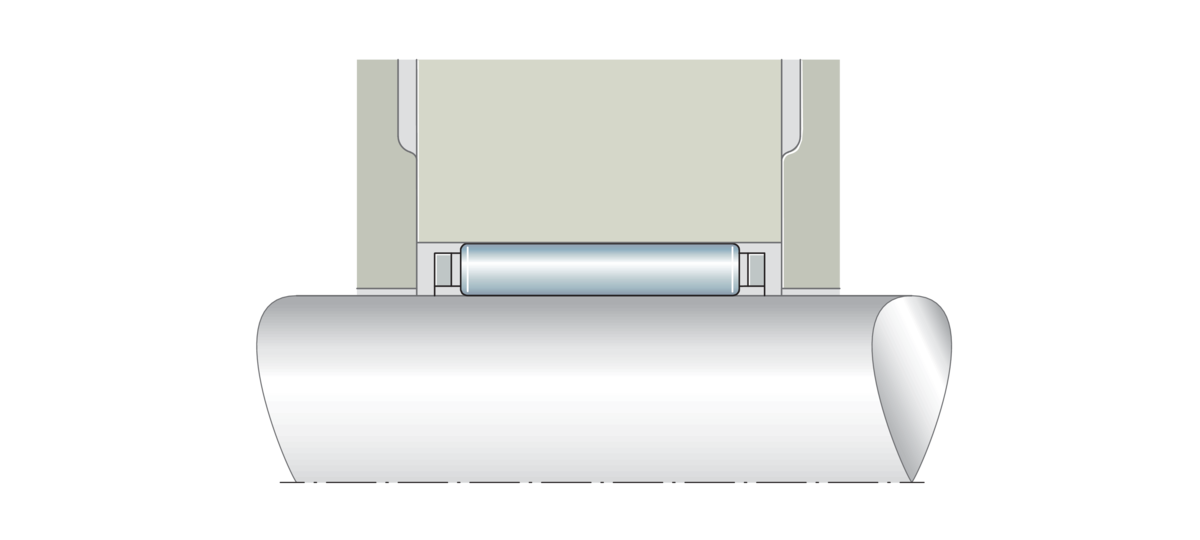 |
Steels for the raceway (direct bearing arrangement)
Through hardening steels
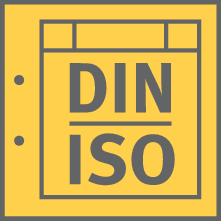
Through hardening steels in accordance with ISO 683-17 (e.g. 100Cr6) are suitable as materials for rolling bearing raceways in direct bearing arrangements. These steels can also be surface layer hardened.
Case hardening steels
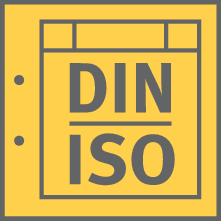
Case hardening steels must correspond to DIN EN ISO 683-17 (e.g. 17MnCr5, 18CrNiMo7-6) or EN 10084 (e.g. 16MnCr5).
Steels for inductive surface layer hardening
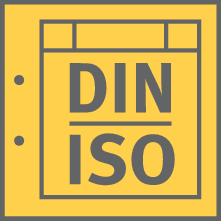
For flame and induction hardening, steels in accordance with DIN EN ISO 683-17 (e.g. C56E2, 43CrMo4) or DIN 17212 (e.g. Cf53) should be used.
Raceway hardness of less than 670 HV
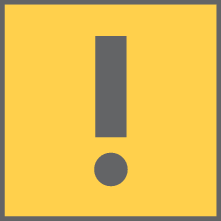
If the raceway fulfils the requirements for rolling bearing materials but the raceway hardness is less than 670 HV, the load on the bearing arrangement cannot be as high as the full load carrying capacity of the bearing. In order to determine the dynamic and static load carrying capacity of the bearing arrangement, the basic dynamic load rating C of the bearings must be multiplied by the reduction factor fH (dynamic hardness factor) and the basic static load rating C0r by the reduction factor fH0 (static hardness factor) ➤ Figure and ➤ Figure.
Dynamic hardness factor at reduced hardness of raceways/rolling elements
fHÂ =Â dynamic hardness factor
HV, HRCÂ =Â surface hardness
|
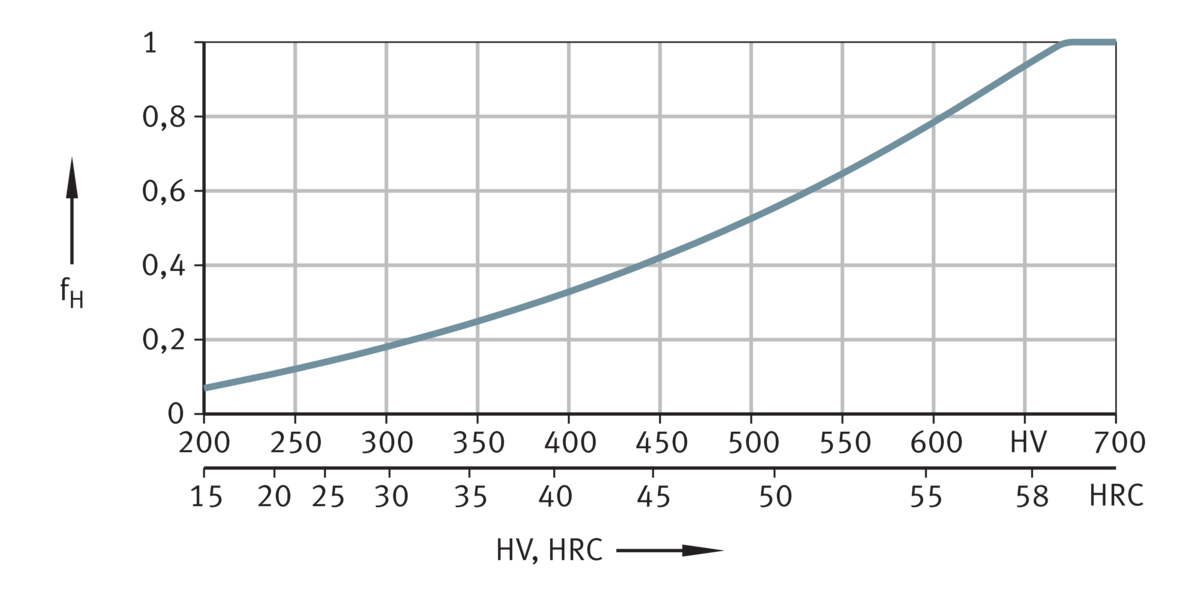 |
Â
Static hardness factor at reduced hardness of raceways/rolling elements
fH0Â =Â static hardness factor
HV, HRCÂ =Â surface hardness
|
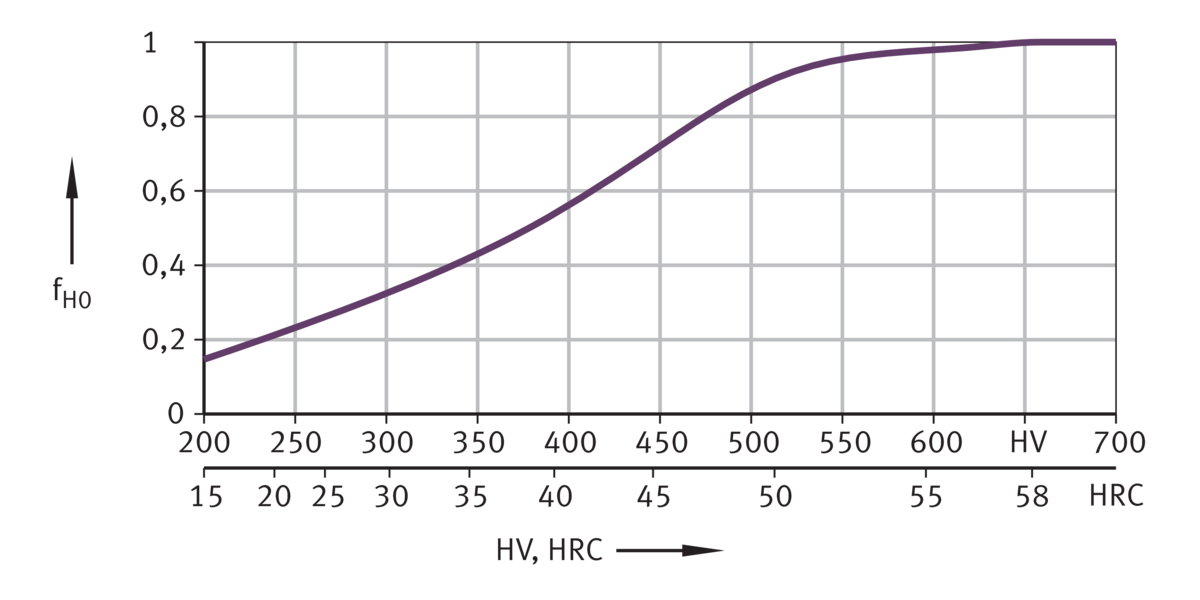 |
Determining the case hardening depth
Approximation value for case hardening depth
An approximation value for determining the minimum hardness depth is given in ➤ Equation. The reference value for the load present is the equivalent stress in accordance with the distortion energy hypothesis (DEH) as a function of the rolling element diameter Dw and the magnitude of the load.
Case hardening depth

Â
Legend
CHD |
mm |
Case hardening depth
|
Dw |
mm |
Rolling element diameter
|
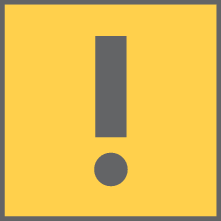
The local hardness must always be above the local requisite hardness, which can be calculated from the equivalent stress.
Determining the surface hardening depth
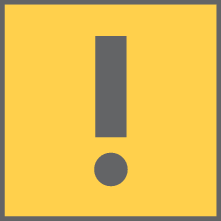
In these surface hardening methods, the load and contact geometry must be taken into consideration when determining the requisite hardening depth.
For calculation of the surface hardening depth SHD ➤ Equation. Â
Surface hardening depth
Legend
SHD |
mm |
Surface hardening depth
|
Dw |
mm |
Rolling element diameter
|
Rp0,2 |
N/mm2 |
Yield point of base material
|
Paired arrangement of needle roller and cage assemblies
The needle rollers must correspond to the same tolerance sort
If two needle roller and cage assemblies are arranged immediately adjacent to each other, it must be ensured that the bearings are loaded uniformly. In this case, the needle rollers used in these needle roller and cage assemblies must belong to the same diameter sort (tolerance sort). The dimensions of the needle rollers fitted in the bearings must be indicated on the specific bearing packaging.
Ensure that the bearings are not damaged during mounting
Needle roller and cage assemblies are either slid onto the shaft and then inserted in the housing or are mounted in the housing and the shaft is then inserted. Mounting is carried out without load and using a screwdriver type motion.
Schaeffler Mounting Handbook
Rolling bearings must be handled with great care
Rolling bearings are well-proven precision machine elements for the design of economical and reliable bearing arrangements, which offer high operational security. In order that these products can function correctly and achieve the envisaged operating life without detrimental effect, they must be handled with care.
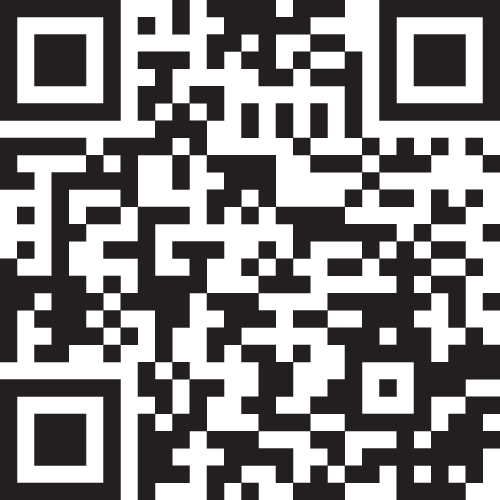
The Schaeffler Mounting Handbook MH 1 gives comprehensive information about the correct storage, mounting, dismounting and maintenance of rotary rolling bearings http://www.schaeffler.de/std/1B68. It also provides information which should be observed by the designer, in relation to the mounting, dismounting and maintenance of bearings, in the original design of the bearing position. This book is available from Schaeffler on request.
The further development of products may also result in technical changes to catalogue products
Of central interest to Schaeffler is the further development and optimisation of its products and the satisfaction of its customers. In order that you, as the customer, can keep yourself optimally informed about the progress that is being made here and with regard to the current technical status of the products, we publish any product changes which differ from the printed version in our electronic product catalogue.
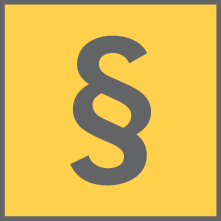
We therefore reserve the right to make changes to the data and illusÂtrations in this catalogue. This catalogue reflects the status at the time of printing. More recent publications released by us (as printed or digital media) will automatically precede this catalogue if they involve the same subject. Therefore, please always use our electronic product catalogue to check whether more up-to-date information or modification notices exist for your desired product.
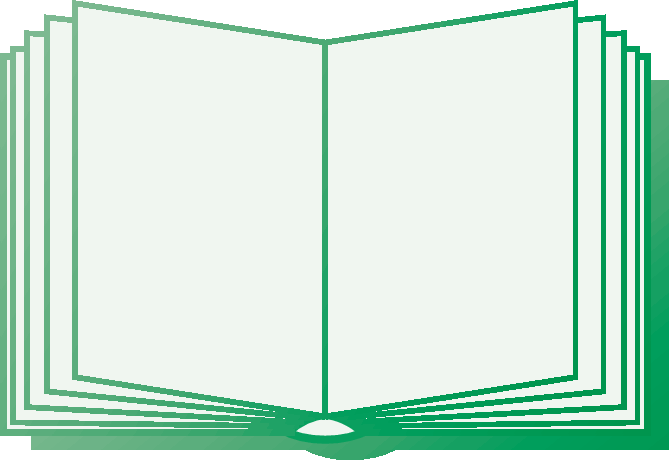
In addition to the data in this chapter, the following chapters in Technical principles must also be observed in the design of bearing arrangements: