Table of contents
Single row angular contact ball bearings
- Bearing design
- Load carrying capacity
- Compensation of angular misalignments
- Lubrication
- Sealing
- Speeds
- Noise
- Temperature range
- Cages
- Internal clearance
- Dimensions, tolerances
- Suffixes
- Structure of bearing designation
- Dimensioning
- Minimum load
- Design of bearing arrangements
- Mounting and dismounting
- Legal notice regarding data freshness
- Further information
Angular contact ball bearings
Single row angular contact ball bearings
Single row angular contact ball bearings are particularly suitable where:
- bearing arrangements must support combined loads, – i.e. radial and axial loads acting simultaneously – ➤ Figure
- moderate to high loads are present on one side
- rigid axial guidance is required
- the bearing arrangement must be axially clearance-free or preloaded
- high speeds are required under higher radial and axial loads
- the bearing arrangement is to run quietly in addition to meeting the requirements stated above
Angular contact ball bearings: nG = limiting speed |
![]() |
Bearing design
Design variants
The standard product range comprises bearings of series 718..-B, 70..‑B(‑2RS), 72..-B(-2RS), 73..-B(-2RS) and 74..-B. These bearings are also available for various applications as:
- bearings of basic design for bearing arrangements with single bearings ➤ Figure
- universal bearings for installation in sets in a tandem, O or X arrangement ➤ Figure, ➤ Figure, ➤ Figure
- X-life bearings ➤ link
Single row angular contact ball bearings are also available in other dimension series, designs and sizes. Information on these bearings is available from Schaeffler on request. Larger catalogue bearings GL 1.
Bearings of basic design for bearing arrangements with single bearings
The forces are transmitted oblique to the radial plane
Single row angular contact ball bearings are part of the group of radial ball bearings. The self-retaining units have solid outer and inner rings. The rolling elements are guided by cages made from polyamide, sheet steel, or brass. The bearing rings are designed with one high shoulder and one low shoulder ➤ Figure. As a result of the different shoulder heights, the mounting method differs from that of deep groove ball bearings. The possible number of balls for angular contact ball bearings with identical dimensions is higher than for deep groove ball bearings. In contrast to deep groove ball bearings, the raceways on the inner and outer rings are arranged obliquely to each other in the direction of the bearing axis. As a result, the forces are transmitted from one raceway to the other at a defined contact angle (oblique to the radial plane) ➤ Figure.
For bearing positions with only one bearing each
These angular contact ball bearings can be considered when only one bearing is used per bearing position. As the bearings have standard bearing ring tolerances (they are manufactured to tolerance class Normal), they are not suitable for mounting directly adjacent to each other. In such cases, universal bearings should be used.
Single row angular contact ball bearing Fr = radial load Fa = axial load α = nominal contact angle |
![]() |
Universal bearings for mounting in sets
Bearings can be mounted in pairs in any arrangement required
Single row angular contact ball bearings, which are intended for mounting in pairs (in sets) directly adjacent to each other, are manufactured in the so-called universal design ➤ Figure, ➤ Figure, ➤ Figure. These bearings can be used in pairs in any arrangement without shims. Depending on the design selected, the mounted bearing pair has the required axial clearance, freedom from clearance or preload. This gives easier design of the bearing arrangement and mounting of the bearings.
When ordering, please state the number of bearings, not the number of bearing pairs.
Suffixes: UA, UB, UO, UL, UM, UH
Bearings of a universal design are indicated by the suffix UA, UB, UO, UL, UM or UH ➤ Table. If bearings of the universal design are arranged in sets, this gives a defined axial clearance or an axial preload:
- UA = bearing set with small axial internal clearance
- UB = bearing set with smaller axial internal clearance than UA
- UO = bearing set clearance-free in O or X arrangement
- UL = bearing set with light preload
- UM = bearing set with moderate preload
- UH = bearing set with high preload
Reasons for mounting in sets
Single row angular contact ball bearings are mounted in sets if:
- the load carrying capacity of one bearing is not sufficient (bearing set in a tandem arrangement)
- combined or axial loads occur in both directions and the bearing arrangement must have a defined axial clearance (bearing set in O or X arrangement)
The following arrangements are possible for mounting in sets:
Bearing sets in tandem arrangement
Tandem arrangement
In a tandem arrangement, the contact lines run parallel to each other ➤ Figure. Axial forces are distributed equally over both bearings, but can only be supported by the bearing set from one direction. In order to support axial forces from the opposing direction, as well as combined loads, the bearing set is always adjusted against a further bearing.
Universal bearings, Bearing set in tandem arrangement |
![]() |
Bearing sets in O arrangement
O arrangement
In an O arrangement, the apexes of the cones formed by the contact lines point outwards, i.e. they diverge relative to the bearing axis ➤ Figure. Bearing sets in an O arrangement support axial forces from both directions, but only ever with one bearing. Due to the large support spacing (i.e. the spacing between the contact cone apexes), these give relatively rigid bearing arrangements (small tilting clearance) and are also suitable for supporting tilting moments.
Universal bearings, Bearing set in O arrangement S = contact cone apex H = support spacing |
![]() |
Bearing sets in X arrangement
X arrangement
In an X arrangement, the apexes of the cones formed by the contact lines point inwards, i.e. they converge relative to the bearing axis ➤ Figure. Once again, bearing sets of this type support axial forces from both directions, but also only ever with one bearing. The support base is, however, smaller than in an O arrangement. As a result, the sets are not as rigid as in an O arrangement. Furthermore, they are less suitable for supporting tilting moments.
Universal bearings, Bearing set in X arrangement H = support spacing |
![]() |
X-life premium quality
Many sizes in series 70..-B, 72..-B, 73..-B and 74..-B are available as X-life bearings ➤ link. These bearings exhibit considerably higher performance than standard single row angular contact ball bearings ➤ Figure. This is achieved, for example, through the modified internal construction, higher surface quality of the contact surfaces and optimised cage design, as well as through the improved quality of the steel and rolling elements.
Advantages
Increased customer benefits due to X-life
The technical enhancements offer a range of advantages, such as:
- a more favourable load distribution in the bearing and thus a higher dynamic load carrying capacity of the bearings ➤ Figure
- quieter running
- running with reduced friction and greater energy efficiency
- lower heat generation in the bearing
- higher possible speeds
- lower lubricant consumption and, consequently, longer maintenance intervals
- a measurably longer operating life of the bearings
- high operational security
- compact, environmentally-friendly bearing arrangements
Lower operating costs, higher machine availability
In conclusion, these advantages improve the overall cost-efficiency of the bearing position significantly and thus bring about a sustainable increase in the efficiency of the machine and equipment.
Suffix XL
Single row X-life angular contact ball bearings include the suffix XL in the designation ➤ Figure, ➤ Figure and ➤ link.
Comparison of basic dynamic load rating Cr = basic dynamic load rating
|
![]() |
Areas of application
Wide application range
Due to their special technical features, single row X-life angular contact ball bearings are highly suitable for bearing arrangements in:
- compressors
- fluid and hydraulic pumps
- automotive chassis and gearboxes
- industrial gearboxes
- electric motors
- industrial ventilators
- machine tools
- textile machinery
X-life indicates a high product performance density and thus a particularly significant benefit to the customer.
Load carrying capacity
Radial load
Single row angular contact ball bearings can support high radial forces. Pure radial loads are also possible, if the bearings are adjusted.
Axial loading is only possible on one side
Due to the geometry and position of the raceway shoulders, axial loads are only transmitted from one direction ➤ Figure. If these angular contact ball bearings are required to support axial forces from both directions, they are adjusted against a second bearing in a mirror image arrangement ➤ Figure and ➤ Figure.
The axial load carrying capacity of the bearings increases with the contact angle
The contact angle α is the angle encompassed by the contact line and the radial plane, under which the load is transmitted from one raceway to the other ➤ Figure. The axial load carrying capacity of the bearing increases with the value of α, i.e. the greater the angle, the higher the axial load to which the bearing can be subjected. As a result, angular contact ball bearings are more suitable than deep groove ball bearings for supporting higher axial forces. Due to the nominal contact angle of α = 40°, single row angular contact ball bearings can support high axial loads on one side.
For information on angular contact ball bearings available with contact angles other than α = 40°, please consult Schaeffler.
Contact angle and force flow α = contact angle
|
![]() |
Load carrying capacity of bearing sets
The basic dynamic and static load ratings Cr and C0r in the product tables always refer to the single bearing. If two bearings of the same size and design are arranged immediately adjacent to each other in an O or X arrangement, the following will apply to the bearing pairs:
- Cr = 1,625 · Cr single bearing
- C0r = 2 · C0r single bearing
Compensation of angular misalignments
The angular adjustment facility of the bearings is very limited
Single row angular contact ball bearings are not suitable for the compensation of angular misalignments. In addition, misalignments induce internal forces in the bearing, which not only lead to higher temperatures, but also to a reduction in the bearing rating life.
Angular contact ball bearings arranged in sets
Misalignments in angular contact ball bearings mounted in sets lead – particularly with a small internal clearance and an O arrangement – to increased loads on the balls and cage, as the angular misalignments are supported under constraint between the balls and raceways. This can, in turn, have a negative effect on the operating life of the bearings. In addition, it should be noted that running noise is increased by a misalignment of the bearing rings.
Lubrication
Greased bearings are maintenance-free
Angular contact ball bearings sealed on both sides are greased with a high quality grease and do not require relubrication.
Ungreased bearings must be lubricated
Open bearings and bearings with seals on one side are not greased. These bearings must be lubricated with oil or grease.
Compatibility with plastic cages
When using bearings with plastic cages, compatibility between the lubricant and the cage material must be ensured if synthetic oils, lubricating greases with a synthetic oil base or lubricants containing a high proportion of EP additives are used.
Observe oil change intervals
Aged oil and additives in the oil can impair the operating life of plastics at high temperatures. As a result, stipulated oil change intervals must be strictly observed.
Sealing
Sealing with contact seals 2RS
Bearings with the suffix 2RS have lip seals on both sides ➤ Table. Due to their good sealing action, they are suitable for use in dusty, contaminated or damp environments.
Open bearings
In the case of unsealed bearings, sealing of the bearing position must be carried out by the adjacent construction. The sealing system should reliably prevent:
- moisture and contaminants from entering the bearing
- the egress of lubricant from the bearing
Speeds
Limiting speeds and reference speeds in the product tables
Two speeds are generally indicated in the product tables:
- the kinematic limiting speed nG
- the thermal speed rating nϑr
Limiting speeds
The limiting speed nG is the kinematically permissible speed of the bearing. Even under favourable mounting and operating conditions, this value should not be exceeded without prior consultation with Schaeffler ➤ link.
The values given in the product tables are valid for oil lubrication in the case of bearings without seals or shields and for grease lubrication where bearings are supplied greased and with seals or shields.
Values for grease lubrication
For grease lubrication, 75% of the value stated in the product tables is permissible in each case.
Reference speeds
nϑr is used to calculate nϑ
The thermal speed rating nϑr is not an application-oriented speed limit, but is a calculated ancillary value for determining the thermally safe operating speed nϑ ➤ link.
Bearings with contact seals
For bearings with contact seals, no speed ratings are defined in accordance with DIN ISO 15312:2004. As a result, only the limiting speed nG is given in the product tables for these bearings.
Bearing sets of universal design
Bearing pairs usually operate at lower speeds than single bearings
Angular contact ball bearings of universal design can be used in an X, O or tandem arrangement ➤ Figure to ➤ Figure. The thermally safe operating speed of the bearing pair is then approximately 20% below the calculated permissible operating speed of the single bearing.
Noise
The Schaeffler Noise Index (SGI) has been developed as a new feature for comparing the noise level of different bearing types and series. As a result, a noise evaluation of rolling bearings can now be carried out for the first time.
Schaeffler Noise Index
The SGI value is based on the maximum permissible noise level of a bearing in accordance with internal standards, which is calculated on the basis of ISO 15242. In order that different bearing types and series can be compared, the SGI value is plotted against the basic static load rating C0.
This permits direct comparisons between bearings with the same load carrying capacity. The upper limit value is given in each of the diagrams. This means that the average noise level of the bearings is lower than illustrated in the diagram.
The Schaeffler Noise Index is an additional performance characteristic in the selection of bearings for noise-sensitive applications. The specific suitability of a bearing for an application in terms of installation space, load carrying capacity or speed limit for example, must be checked independently of this.
Schaeffler Noise Index SGI = Schaeffler Noise Index C0 = basic static load rating |
![]() |
Temperature range
Limiting values
The operating temperature of the bearings is limited by:
- the dimensional stability of the bearing rings and rolling elements
- the cage
- the lubricant
- the seals
Possible operating temperatures of single row angular contact ball bearings ➤ Table.
Permissible temperature ranges
Operating temperature |
Single row angular contact ball bearings, open |
Single row angular contact ball bearings, sealed |
|
---|---|---|---|
with sheet steel or brass cage |
with polyamide cage PA66 |
||
|
–30 °C to +150 °C, |
–30 °C to +120 °C |
–30 °C to +110 °C, limited by the lubricant and seal material |
In the event of anticipated temperatures which lie outside the stated values, please contact Schaeffler.
Cages
Solid cages made from brass and PA66, as well as sheet steel cages, are used as standard
Standard cages and additional cage designs for single row angular contact ball bearings are made from brass, polyamide or steel ➤ Table. Other cages are available by agreement. With such cages, however, suitability for high speeds and temperatures as well as the basic load ratings may differ from the values for the bearings with standard cages.
For high continuous temperatures and applications with difficult operating conditions, bearings with brass or sheet steel cages should be used. If there is any uncertainty regarding cage suitability, please consult Schaeffler.
Cage, cage suffix, bore code
Bearing series |
Solid cage |
Solid cage |
Sheet steel cage |
||
---|---|---|---|---|---|
TVH, TVP |
MP |
JP |
|||
standard |
also |
standard |
also |
also |
|
Bore code |
|||||
718 |
06 to 16 |
‒ |
‒ |
‒ |
‒ |
70 |
04 to 08 |
‒ |
‒ |
‒ |
‒ |
72 |
up to 20, |
‒ |
21, |
00, 03, |
up to 20, 22 |
73 |
up to 20, |
‒ |
21, |
from 04 |
up to 20, 22 |
74 |
‒ |
07 to 15 |
05 to 16 |
‒ |
07 to 15 |
Internal clearance
Axial internal clearance, preload and preload force of bearing sets with universal bearings in O or X arrangement
Valid for bearing sets in O or X arrangement
Values for axial internal clearance, preload and preload force of bearings of universal design ➤ Table. The values for axial internal clearance are valid for unmounted bearing sets in an O or X arrangement, which are free from load and measurement forces (without elastic deformation).
The angular contact ball bearings can also be supplied with a different internal clearance. Please consult Schaeffler in this case.
Axial internal clearance, preload and preload force of bearing sets with universal bearings in O or X arrangement for tolerance classes Normal, 6, 5
Bore code |
Axial internal clearance or preload Nominal dimension |
Preload force FV max |
|||||||||
---|---|---|---|---|---|---|---|---|---|---|---|
μm |
N |
||||||||||
UA |
UB |
UO |
UL |
UL |
|||||||
Bearing series |
|||||||||||
70..-B, 72..-B, 73..-B, 74..-B |
70..-B |
72..-B |
73..-B |
74..-B |
70..-B |
72..-B |
73..-B |
74..-B |
|||
00 |
22 |
14 |
0 |
‒ |
–3 |
‒ |
‒ |
‒ |
38 |
‒ |
‒ |
01 |
24 |
15 |
0 |
‒ |
–4 |
–5 |
‒ |
‒ |
53 |
82 |
‒ |
02 |
24 |
15 |
0 |
‒ |
–4 |
–5 |
‒ |
‒ |
62 |
99 |
‒ |
03 |
24 |
15 |
0 |
‒ |
–4 |
–6 |
‒ |
‒ |
77 |
123 |
‒ |
04 |
28 |
16 |
0 |
–4 |
–5 |
–6 |
–8 |
103 |
103 |
146 |
258 |
05 |
34 |
19 |
0 |
–4 |
–4 |
–6 |
–8 |
115 |
112 |
200 |
300 |
06 |
34 |
19 |
0 |
–5 |
–5 |
–7 |
–8 |
141 |
157 |
250 |
365 |
07 |
40 |
22 |
0 |
–5 |
–6 |
–7 |
–9 |
172 |
208 |
300 |
462 |
08 |
40 |
22 |
0 |
–5 |
–6 |
–8 |
–10 |
200 |
246 |
385 |
535 |
09 |
44 |
24 |
0 |
‒ |
–6 |
–9 |
–10 |
‒ |
277 |
462 |
600 |
10 |
44 |
24 |
0 |
‒ |
–6 |
–10 |
–10 |
‒ |
288 |
535 |
692 |
11 |
46 |
25 |
0 |
‒ |
–7 |
–10 |
–11 |
‒ |
358 |
600 |
785 |
12 |
46 |
25 |
0 |
‒ |
–7 |
–10 |
–11 |
‒ |
431 |
692 |
877 |
13 |
46 |
25 |
0 |
‒ |
–8 |
–11 |
–12 |
‒ |
492 |
785 |
977 |
14 |
50 |
27 |
0 |
‒ |
–8 |
–11 |
–12 |
‒ |
535 |
877 |
1 154 |
15 |
50 |
27 |
0 |
‒ |
–8 |
–12 |
–13 |
‒ |
523 |
977 |
1 154 |
16 |
50 |
27 |
0 |
‒ |
–8 |
–12 |
–16 |
‒ |
615 |
1 077 |
1 385 |
17 |
54 |
31 |
0 |
‒ |
–8 |
–13 |
‒ |
‒ |
692 |
1 154 |
‒ |
18 |
54 |
31 |
0 |
‒ |
–9 |
–13 |
‒ |
‒ |
815 |
1 231 |
‒ |
19 |
54 |
31 |
0 |
‒ |
–10 |
–14 |
‒ |
‒ |
892 |
1 331 |
‒ |
20 |
54 |
31 |
0 |
‒ |
–11 |
–14 |
‒ |
‒ |
992 |
1 485 |
‒ |
21 |
58 |
34 |
0 |
‒ |
–11 |
–14 |
‒ |
‒ |
1 100 |
1 538 |
‒ |
22 |
58 |
34 |
0 |
‒ |
–12 |
–15 |
‒ |
‒ |
1 177 |
1 723 |
‒ |
24 |
58 |
34 |
0 |
‒ |
–12 |
–16 |
‒ |
‒ |
1 277 |
1 923 |
‒ |
26 |
60 |
34 |
0 |
‒ |
–12 |
–17 |
‒ |
‒ |
1 431 |
2 115 |
‒ |
28 |
60 |
34 |
0 |
‒ |
–12 |
–17 |
‒ |
‒ |
1 508 |
2 308 |
‒ |
30 |
60 |
34 |
0 |
‒ |
–13 |
–18 |
‒ |
‒ |
1 723 |
2 500 |
‒ |
32 |
60 |
34 |
0 |
‒ |
–13 |
–18 |
‒ |
‒ |
1 815 |
2 769 |
‒ |
34 |
70 |
40 |
0 |
‒ |
–14 |
–19 |
‒ |
‒ |
2 038 |
3 115 |
‒ |
UA = bearing with small axial internal clearance
UB = bearing with smaller axial internal clearance than UA
UO = bearing clearance-free in O or X arrangement
UL = bearing with light preload
Tolerances for axial internal clearance and preload
Tolerances for axial internal clearance and preload of bearing sets with universal bearings in O and X arrangement ➤ Table.
Tolerances for axial internal clearance and preload of bearing sets with universal bearings in O or X arrangement
Bore code |
Tolerances |
|||||
---|---|---|---|---|---|---|
μm |
||||||
Bearing series |
||||||
70..-B, 72..-B |
73..-B |
74..-B |
||||
Tolerance class |
||||||
Normal, 6 |
5 |
Normal, 6 |
5 |
Normal, 6 |
5 |
|
00 to 07 |
+8 0 |
+6 0 |
+8 0 |
+6 0 |
+8 0 |
+6 0 |
08 to 09 |
+8 0 |
+6 0 |
+8 0 |
+6 0 |
+12 0 |
+10 0 |
10 to 11 |
+8 0 |
+6 0 |
+12 0 |
+10 0 |
+12 0 |
+10 0 |
12 to 34 |
+12 0 |
+10 0 |
+12 0 |
+10 0 |
+12 0 |
+10 0 |
Dimensions, tolerances
Dimension standards
The main dimensions of angular contact ball bearings of the basic design correspond to DIN 628-1:2008 and ISO 12044:2014. Nominal dimensions of angular contact ball bearings ➤ link.
Chamfer dimensions
The limiting dimensions for chamfer dimensions correspond to DIN 620‑6:2004. Overview and limiting values ➤ section. Nominal value of chamfer dimension ➤ link.
Tolerances
The tolerances for the dimensional and running accuracy of single row angular contact ball bearings correspond to tolerance class Normal in accordance with ISO 492:2014. Tolerance values in accordance with ISO 492 ➤ link and ➤ link.
Tolerances for bearings of universal design
Single row bearings are also available in tolerance class 5
In addition to the tolerance class Normal (no tolerance suffix), angular contact ball bearings of universal designs UA, UB, UO and UL are also available by agreement in tolerance class 5 and, in some cases, in tolerance class 6. Tolerance values in accordance with ISO 492 ➤ link. The tolerance suffix for bearings of universal design in tolerance class 5 is then:
- P5-UA, P5-UB, P5-UO, P5-UL
The bores of bearings of universal design for all tolerance classes are uniformly toleranced to tolerance class 5 (no special suffix). The bearing width for universal bearings is toleranced to ISO 492:2014. For width tolerances see ➤ Table.
Tolerance for ring width in bearings of universal design
Nominal bore diameter |
Width deviation |
||||
---|---|---|---|---|---|
d |
tΔBs |
||||
mm |
μm |
||||
Bearings in tolerance class |
|||||
Normal, 6 |
5 |
||||
over |
incl. |
U |
L |
U |
L |
‒ |
50 |
0 |
–250 |
0 |
–250 |
50 |
80 |
0 |
–380 |
0 |
–250 |
80 |
120 |
0 |
–380 |
0 |
–380 |
120 |
180 |
0 |
–500 |
0 |
–380 |
180 |
315 |
0 |
–500 |
0 |
–500 |
Tolerance symbols ➤ link
U = upper limit deviation
L = lower limit deviation
Suffixes
For a description of the suffixes used in this chapter see ➤ Table and medias interchange http://www.schaeffler.de/std/1B69.
Suffixes and corresponding descriptions
Suffix |
Description of suffix |
|
---|---|---|
B |
Modified internal construction, nominal contact angle α = 40° |
Standard |
JP |
Sheet steel cage |
Standard, dependent on bore code |
MP |
Solid brass cage |
Standard, dependent on bore code |
TVH, TVP |
Solid cage made from glass fibre reinforced polyamide PA66 |
Standard, dependent on bore code |
P5 |
Bearing in tolerance class 5 |
Special design, available by agreement |
2RS |
Contact seal on both sides (lip seal) |
Standard |
UA |
Universal design for fitting in pairs, bearing pair has a small axial internal clearance in O and X arrangement |
Standard |
UB |
Universal design for fitting in pairs, bearing pair has a smaller axial internal clearance in O and X arrangement than in UA |
Standard |
UH |
Universal design for fitting in pairs, bearing pair has a high preload in O and X arrangement |
Available by agreement |
UL |
Universal design for fitting in pairs, bearing pair has a light preload in O and X arrangement |
Standard |
UM |
Universal design for fitting in pairs, bearing pair has a moderate preload in O and X arrangement |
Available by agreement |
UO |
Universal design for fitting in pairs, bearing pair is clearance-free in O and X arrangement |
Standard |
XL |
X-life bearing, dependent on bore code and bearing type |
Standard |
Structure of bearing designation
Examples of composition of bearing designation
The designation of bearings follows a set model. Examples ➤ Figure and ➤ Figure. The composition of designations is subject to DIN 623‑1 ➤ link.
Single row angular contact ball bearing |
![]() |
Single row angular contact ball bearing |
![]() |
Dimensioning
Equivalent dynamic bearing load
P = Fr under purely radial load of constant magnitude and direction
The basic rating life equation L = (Cr/P)p used in the dimensioning of bearings under dynamic load assumes a load of constant magnitude and direction. In radial bearings, this is purely radial load Fr. If this condition is met, the bearing load Fr is used directly in the rating life equation for P (P = Fr).
P is a substitute force for combined load and various load cases
If this condition is not met, a constant radial force must first be determined for the rating life calculation that (in relation to the rating life) represents an equivalent load. This force is known as the equivalent dynamic load P.
Fa/Fr ≦ 1,14 or Fa/Fr > 1,14
The calculation of P is dependent on the load ratio Fa/Fr and the factor 1,14.
Tandem arrangement
For single bearings under dynamic load and bearing pairs in a tandem arrangement see ➤ Equation and ➤ Equation.
Equivalent dynamic load
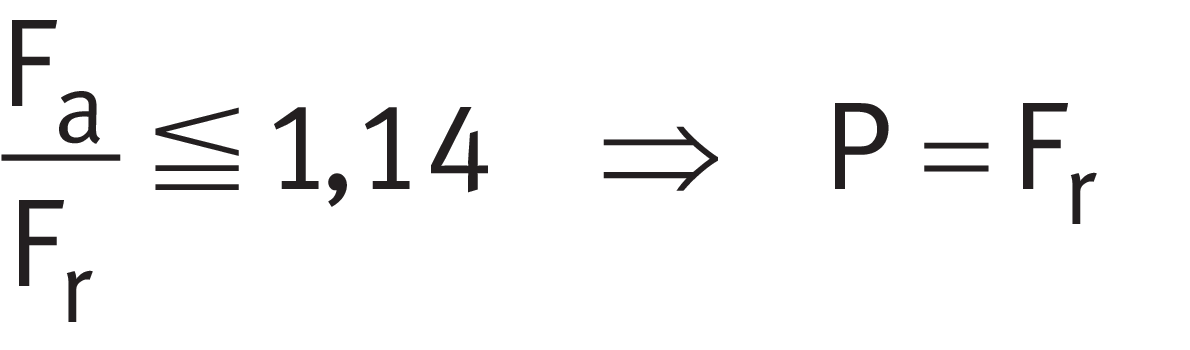
Equivalent dynamic load

Legend
P | N |
Equivalent dynamic bearing load |
Fr | N |
Radial load |
Fa | N |
Resulting axial force ➤ Table. The information in the section “Calculation of internal resulting axial force Fa for single bearings and for bearings in a tandem arrangement” must be taken into consideration when calculating Fa ➤ link |
Bearing pairs in O or X arrangement
For bearing pairs under dynamic load in O or X arrangement see ➤ Equation and ➤ Equation.
Equivalent dynamic load

Equivalent dynamic load

Legend
P | N |
Equivalent dynamic bearing load |
Fr | N |
Radial load |
Fa | N |
Resulting axial force ➤ Equation and ➤ Table |
Calculation of internal resulting axial force Fa for single bearings and for bearings in a tandem arrangement
Equations for calculation of internal resulting axial force Fa
Single row angular contact ball bearings transmit radial forces from one raceway to the other oblique to the bearing axis. In the case of a shaft supported by two single row angular contact ball bearings of identical or different size, the radial load on bearing A therefore leads, due to the inclination of the raceways (α ≠ 0°), to an axial load on bearing B. The radial load on bearing B also has the effect of an axial load on bearing A; external forces in bearing systems of this type ➤ Figure and ➤ Figure. This internal resulting axial force Fa must be taken into consideration in the calculation of the equivalent dynamic bearing load P. Equations for calculation of resulting axial force Fa ➤ Table. The table shows the magnitude of the resulting axial force – that is the sum of or the difference between the internal and external axial force – for bearing arrangements in accordance with ➤ Figure and ➤ Figure. The following applies to the table: the bearing aligned to the external axial force Ka is marked A and the opposing bearing is marked B.
Preconditions for calculation
Bearing A is subjected to a radial load FrA, bearing B to a radial load FrB ➤ Figure and ➤ Figure. FrA and FrB act at the central pressure points of the bearings (dimension a in the product tables) and are always regarded as positive. The bearings are clearance-free, but without preload.
Calculation of internal resulting axial force Fa
Case |
Load ratio |
External axial force |
Resulting axial force Fa |
|
---|---|---|---|---|
Bearing A |
Bearing B |
|||
1 |
|
Ka ≧ 0 |
|
Fa is not taken into consideration in the calculation |
2 |
|
|
|
Fa is not taken into consideration in the calculation |
3 |
|
|
Fa is not taken into consideration in the calculation |
|
Fa = internal resulting axial force, which must be used in the calculation of the equivalent dynamic bearing load P.
YA = YB = 0,57
Adjusted bearing arrangement Ka = external axial force acting on the bearing FrA = radial load, bearing A FrB = radial load, bearing B |
![]() |
Adjusted bearing arrangement Ka = external axial force acting on the bearing FrA = radial load, bearing A FrB = radial load, bearing B |
![]() |
Example of calculation of internal resulting axial force Fa
Bearing arrangement for pinion shaft
Single row angular contact ball bearings are used for the bearing arrangement of a pinion shaft ➤ Figure. The bearing arrangement should be adjusted and in an O arrangement. In order to calculate the basic rating life, the equivalent dynamic bearing load P must be determined.
Load scheme for pinion shaft Ka = external axial force = 6,52 kN Kr = external radial force = 0,82 kN Kt = tangential force = 5,88 kN Resulting radial forces Fr Bearing A, FrA = 7,30 kN Bearing B, FrB = 2,20 kN |
![]() |
In a bearing arrangement with two single bearings, the resulting axial force Fa must be taken into consideration
Bearing A supports the external axial force Ka. Since this is an adjusted bearing arrangement with two single bearings, the internal resulting axial force Fa in the bearing system must be taken into consideration in the bearing calculation in accordance with ➤ Table. For both angular contact ball bearings YA = YB = 0,57. Loads ➤ Figure.
Step 1
Calculate the load ratio using ➤ Equation.
Load ratio
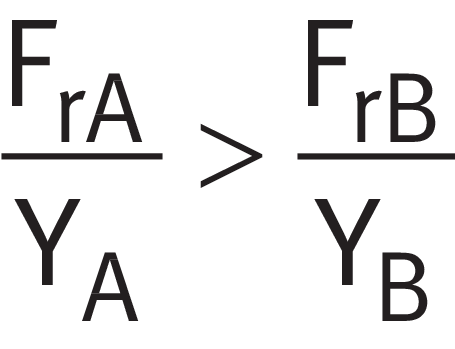
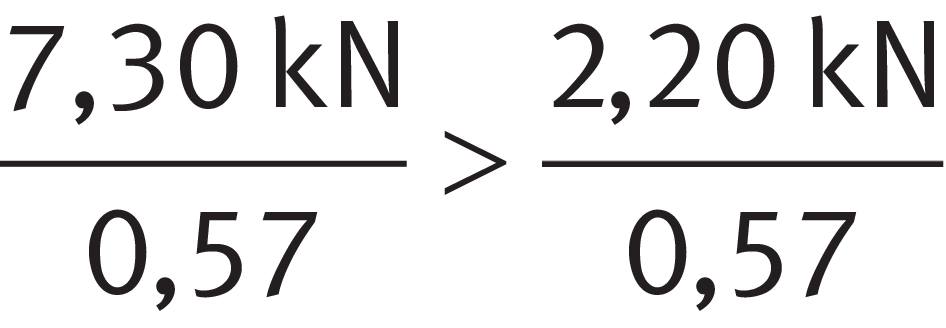
Step 2
Compare the result with possible cases ➤ Table. Case 2 or case 3 can be considered ➤ Table.
Calculation of internal resulting axial force Fa
Case |
Load ratio |
External axial force |
Resulting axial force Fa |
|
---|---|---|---|---|
Bearing A |
Bearing B |
|||
2 | ![]() |
|
|
‒ |
3 | ![]() |
|
‒ |
|
Parameters ➤ Equation
YA = YB = 0,57
Step 3
Using ➤ Equation, check whether case 2 applies ➤ Table.
External axial force in relation to load ratio
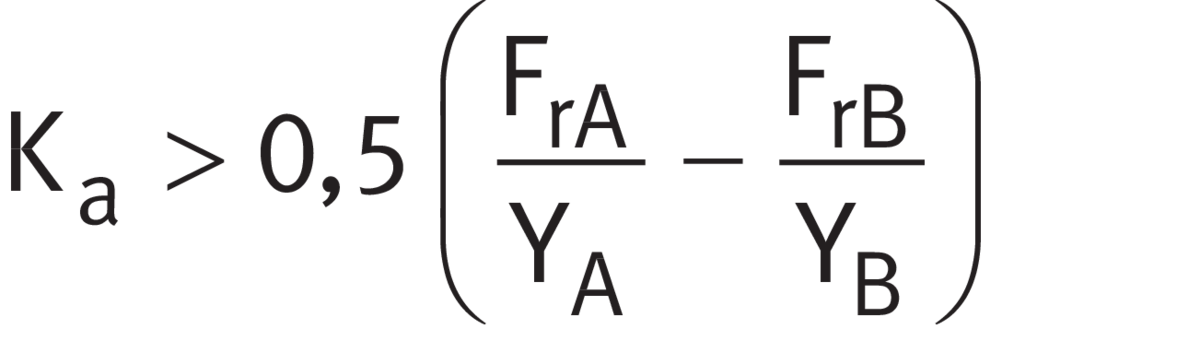
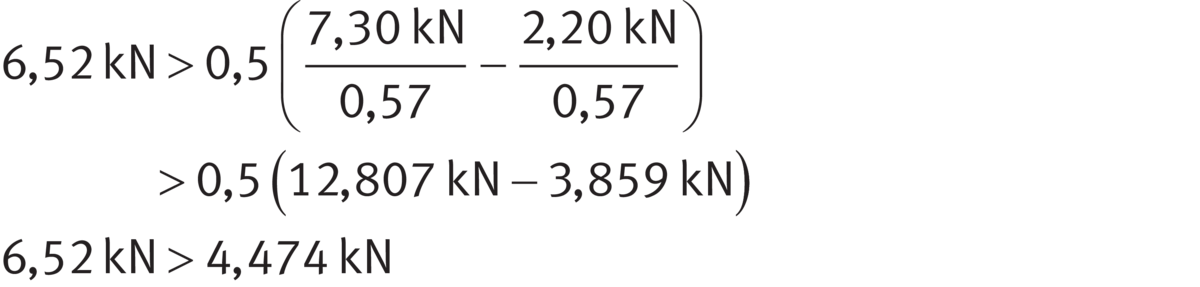
Case 2 applies ➤ Table.
Step 4
Calculating Fa
Using ➤ Equation, calculate the internal resulting axial force Fa for bearing A. The calculations are in accordance with ➤ Table, case 2.
Internal resulting axial force
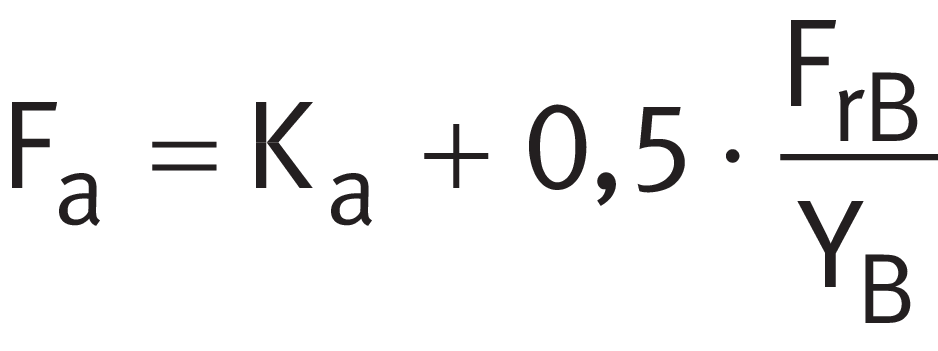
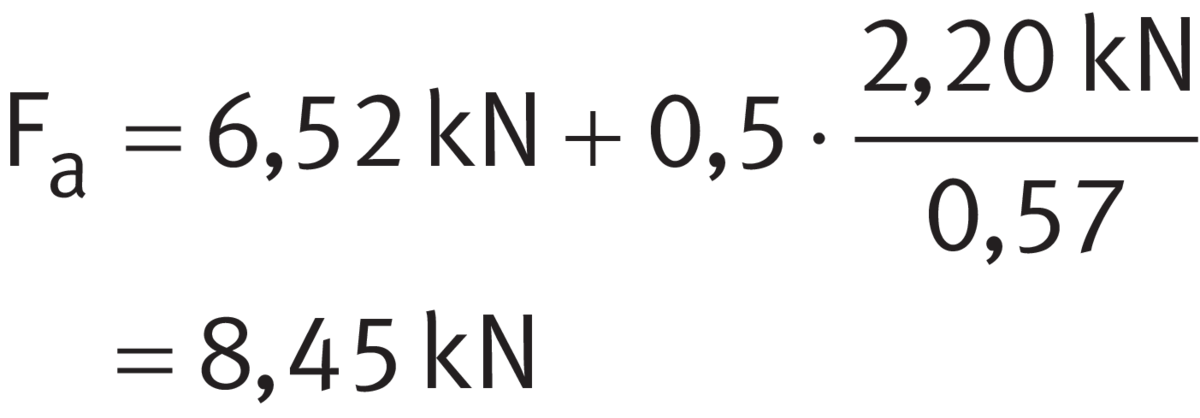
Using value Fa in the calculation of P
For calculation of the equivalent dynamic bearing load P, the calculated value for Fa in ➤ Equation is then used for bearing A, since Fa/FrA > 1,14 (8,45 kN/7,30 kN > 1,14).
Equivalent static bearing load
Tandem arrangement
For single bearings under static load and bearing pairs in a tandem arrangement see ➤ Equation and ➤ Equation.
Equivalent static load
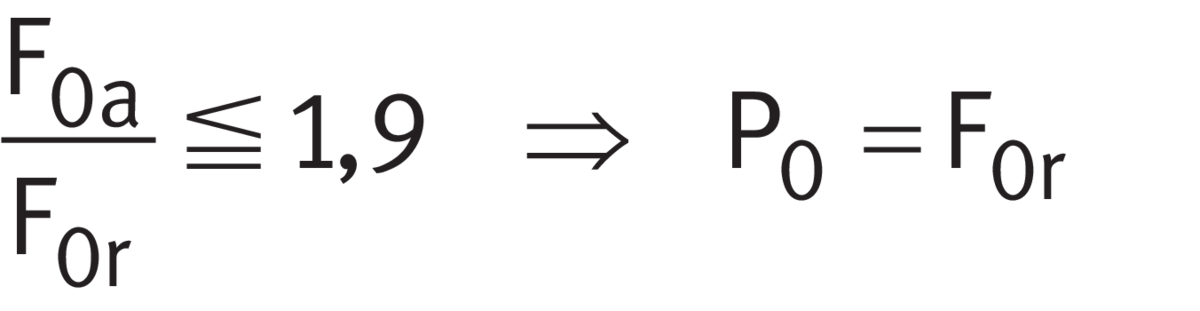
Equivalent static load

Legend
P0 | N |
Equivalent static bearing load |
F0r, F0a | N |
Largest radial or axial load present (maximum load) |
For bearing pairs under static load in an O or X arrangement see ➤ Equation.
Equivalent static load

Legend
P0 | N |
Equivalent static bearing load |
F0r, F0a | N |
Largest radial or axial load present (maximum load) |
Static load safety factor
S0 = C0/P0
In addition to the basic rating life L (L10h), it is also always necessary to check the static load safety factor S0 ➤ Equation.
Static load safety factor
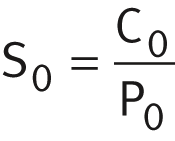
Legend
S0 | - |
Static load safety factor |
C0 | N |
Basic static load rating |
P0 | N |
Equivalent static bearing load |
Minimum load
In order to prevent damage due to slippage, a minimum radial load of P > C0r/100 is required
In order that no slippage occurs between the contact partners, the angular contact ball bearings must be constantly subjected to a sufficiently high load. Based on experience, a minimum radial load of the order of P > C0r/100 is thus necessary. In most cases, however, the radial load is already higher than the requisite minimum load due to the weight of the supported parts and the external forces.
If the minimum radial load is lower than indicated above, please consult Schaeffler.
Design of bearing arrangements
Support bearing rings over their entire circumference and width
In order to allow full utilisation of the load carrying capacity of the bearings and thus also achieve the requisite rating life, the bearing rings must be rigidly and uniformly supported by means of contact surfaces over their entire circumference and over the entire width of the raceway. Support can be provided by means of a cylindrical seating surface. The seating and contact surfaces should not be interrupted by grooves, holes or other recesses. The accuracy of mating parts must meet specific requirements ➤ link.
Radial location of bearings – fit recommendations
For secure radial location, tight fits are necessary
In addition to supporting the rings adequately, the bearings must also be securely located in a radial direction, to prevent creep of the bearing rings on the mating parts under load. This is generally achieved by means of tight fits between the bearing rings and the mating parts. If the rings are not secured adequately or correctly, this can cause severe damage to the bearings and adjacent machine parts. Influencing factors, such as the conditions of rotation, magnitude of the load, internal clearance, temperature conditions, design of the mating parts and the mounting and dismounting options must be taken into consideration in the selection of fits.
If shock type loads occur, tight fits (transition fit or interference fit) are required to prevent the rings from coming loose at any point. Clearance, transition or interference fits ➤ link.
The following information provided in Technical principles must be taken into consideration in the design of bearing arrangements:
- conditions of rotation ➤ link
- tolerance classes for cylindrical shaft seats (radial bearings) ➤ link
- shaft fits ➤ link
- tolerance classes for bearing seats in housings (radial bearings) ➤ link
- housing fits ➤ link
Axial location of bearings – location methods
The bearings must also be securely located in an axial direction
As a tight fit alone is not normally sufficient to also locate the bearing rings securely on the shaft and in the housing bore in an axial direction, this must usually be achieved by means of an additional axial location or retention method. The axial location of the bearing rings must be matched to the type of bearing arrangement. Shaft and housing shoulders, housing covers, nuts, spacer rings and retaining rings etc., are fundamentally suitable ➤ Figure and ➤ Figure.
Dimensional, geometrical and running accuracy of the bearing seats
A minimum of IT6 should be provided for the shaft seat and a minimum of IT7 for the housing seat
The accuracy of the bearing seat on the shaft and in the housing should correspond to the accuracy of the bearing used. For single row angular contact ball bearings with the tolerance class Normal, the shaft seat should correspond to a minimum of standard tolerance grade IT6 and the housing seat to a minimum of IT7; with tolerance class 6, the shaft seat should correspond to a minimum of IT5 and the housing seat to IT6. Guide values for the geometrical and positional tolerances of bearing seating surfaces ➤ Table, tolerances t1to t3 in accordance with ➤ Figure. Numerical values for IT grades ➤ Table.
Guide values for the geometrical and positional tolerances of bearing seating surfaces
Bearing |
Bearing seating surface |
Standard tolerance grades to ISO 286-1 |
||||
---|---|---|---|---|---|---|
to ISO 492 |
to DIN 620 |
Diameter tolerance |
Roundness tolerance |
Parallelism tolerance |
Total axial runout tolerance of abutment shoulders |
|
t1 |
t2 |
t3 |
||||
Normal |
PN (P0) |
Shaft |
IT6 (IT5) |
Circumferential load IT4/2 |
Circumferential load IT4/2 |
IT4 |
Shaft | IT6 (IT5) |
Point load IT5/2 |
Point load IT5/2 |
IT4 | ||
Housing |
IT7 (IT6) |
Circumferential load IT5/2 |
Circumferential load IT5/2 |
IT5 |
||
Housing | IT7 (IT6) |
Point load IT6/2 |
Point load IT6/2 |
IT5 | ||
6 |
P6 |
Shaft |
IT5 |
Circumferential load IT3/2 |
Circumferential load IT3/2 |
IT3 |
Shaft | IT5 |
Point load IT4/2 |
Point load IT4/2 |
IT3 | ||
Housing |
IT6 |
Circumferential load IT4/2 |
Circumferential load IT4/2 |
IT4 |
||
Housing | IT6 |
Point load IT5/2 |
Point load IT5/2 |
IT4 |
Numerical values for ISO standard tolerances (IT grades) to ISO 286-1:2010
IT grade |
Nominal dimension in mm |
||||||||
---|---|---|---|---|---|---|---|---|---|
over |
3 |
6 |
10 |
18 |
30 |
50 |
80 |
120 |
|
incl. |
6 |
10 |
18 |
30 |
50 |
80 |
120 |
180 |
|
Values in μm |
|||||||||
IT3 |
2,5 | 2,5 | 3 | 4 | 4 | 5 | 6 | 8 | |
IT4 |
4 | 4 | 5 | 6 | 7 | 8 | 10 | 12 | |
IT5 |
5 | 6 | 8 | 9 | 11 | 13 | 15 | 18 | |
IT6 |
8 | 9 | 11 | 13 | 16 | 19 | 22 | 25 | |
IT7 |
12 | 15 | 18 | 21 | 25 | 30 | 35 | 40 |
Roughness of cylindrical bearing seats
Ra must not be too high
The roughness of the bearing seats must be matched to the tolerance class of the bearings. The mean roughness value Ra must not be too high, in order to maintain the interference loss within limits. The shafts must be ground, while the bores must be precision turned. Guide values as a function of the IT grade of bearing seating surfaces ➤ Table.
Roughness values for cylindrical bearing seating surfaces – guide values
Nominal diameter d (D) |
Recommended mean roughness value Ramax |
||||
---|---|---|---|---|---|
mm |
μm |
||||
Diameter tolerance (IT grade) |
|||||
over |
incl. |
IT7 |
IT6 |
IT5 |
IT4 |
‒ |
80 |
1,6 |
0,8 |
0,4 |
0,2 |
80 |
500 |
1,6 |
1,6 |
0,8 |
0,4 |
Mounting dimensions for the contact surfaces of bearing rings
The contact surfaces for the rings must be of sufficient height
The mounting dimensions of the shaft and housing shoulders, and spacer rings etc., must ensure that the contact surfaces for the bearing rings are of sufficient height. However, they must also reliably prevent rotating parts of the bearing from grazing stationary parts.Proven mounting dimensions for the radii and diameters of abutment shoulders ➤ link. These dimensions are limiting dimensions (maximum or minimum dimensions); the actual values should not be higher or lower than specified.
If single row angular contact bearings are mounted in a tandem arrangement, it must be ensured that the end faces of the outer rings in contact with each other have sufficient overlap. In case of doubt, please consult Schaeffler.
Adjustment of bearings
Always adjust single bearings against a second bearing
Single row angular contact ball bearings must always be used with a second bearing or as a bearing set ➤ Figure. If two individual single row angular contact ball bearings are used, these must be adjusted against each other until the requisite preload or desired clearance is achieved.
Select the adjustment such that full function and operational reliability of the bearings is ensured
The correct adjustment of the bearings has a considerable influence on the function and operational reliability of the bearing arrangement. If the clearance is too large, the load carrying capacity of the bearings will not be fully utilised; if the preload is too high, the increased friction losses will give rise to higher operating temperatures, which will, in turn, have a negative effect on the rating life of the bearings.
Adjusted bearing arrangement
|
![]() |
Adjustment not required for bearing sets
Universal bearings arranged immediately adjacent to each other, or matched bearings, do not need to be adjusted. In such cases, the desired operating clearance or required preload is achieved by selecting the internal clearance or preload class in conjunction with the suitable shaft and housing fits. As a result, particular attention must be paid to the correct selection of internal clearance or preload for these bearing sets.
Mounting and dismounting
The mounting and dismounting options for angular contact ball bearings, by thermal, hydraulic or mechanical methods, must be taken into consideration in the design of the bearing position.
Ensure that the bearings are not damaged during fitting
Single row angular contact ball bearings are not separable. In the mounting of such bearings, the mounting forces must always be applied to the bearing ring with a tight fit.
Schaeffler Mounting Handbook
Rolling bearings must be handled with great care
Rolling bearings are well-proven precision machine elements for the design of economical and reliable bearing arrangements, which offer high operational security. In order that these products can function correctly and achieve the envisaged operating life without detrimental effect, they must be handled with care.
The Schaeffler Mounting Handbook MH 1 gives comprehensive information about the correct storage, mounting, dismounting and maintenance of rotary rolling bearings http://www.schaeffler.de/std/1B68. It also provides information which should be observed by the designer, in relation to the mounting, dismounting and maintenance of bearings, in the original design of the bearing position. This book is available from Schaeffler on request.
Legal notice regarding data freshness
The further development of products may also result in technical changes to catalogue products
Of central interest to Schaeffler is the further development and optimisation of its products and the satisfaction of its customers. In order that you, as the customer, can keep yourself optimally informed about the progress that is being made here and with regard to the current technical status of the products, we publish any product changes which differ from the printed version in our electronic product catalogue.
We therefore reserve the right to make changes to the data and illustrations in this catalogue. This catalogue reflects the status at the time of printing. More recent publications released by us (as printed or digital media) will automatically precede this catalogue if they involve the same subject. Therefore, please always use our electronic product catalogue to check whether more up-to-date information or modification notices exist for your desired product.
Further information
In addition to the data in this chapter, the following chapters in Technical principles must also be observed in the design of bearing arrangements: